- SMT Assembly, BGA Assembly, Through hole Assembly, Mixed Assembly
- PCB assembly or Box build assembly service delivers a PCBA or a complete electronics assembly in a box
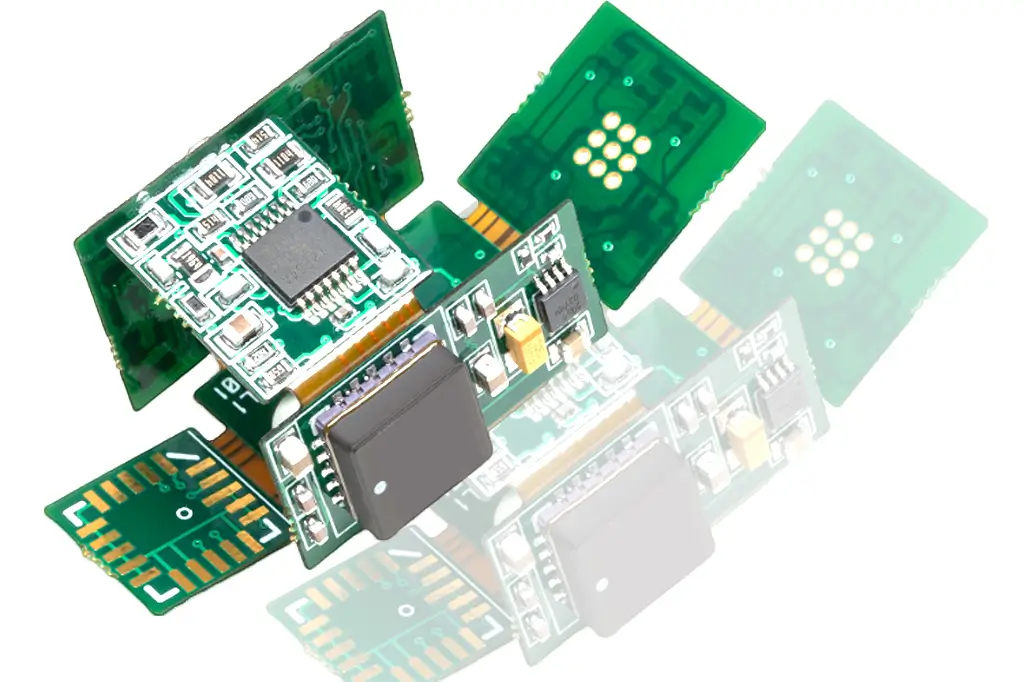
Rigid flex PCB Assembly
During rigid-flex assembly, components will be mounted on both the rigid and flex regions. A rigidized flex circuit is nothing but a flex PCB with an FR4 stiffener added to strengthen the rigidity during assembly. The layers of rigid flex connect to one another electrically through vias.
Generally, these PCBs have multi-layer options. The important aspect here is that the flex layers in these boards are always placed at the center of the stack-up. This provides mechanical support for the flex layers during the assembly process.

Rigid flex PCB Assembly Capabilities
We pride ourselves on the ability to take on complex jobs — from fabrication to assembly — all under one roof with state-of-the-art technology, including a new selective soldering machine.
Our engineering team uses best practices for flex and rigid-flex pcb assembly, and our operators understand how to properly assemble flex circuits to avoid delamination.
- Surface mount technology (SMT)
- Through hole
- Flip chip
- In-circuit testing (ICT) and flying probe testing
- X-ray inspection
- Press fit
- Conformal coating
- Automatic Optical Inspection (AOI)
- Selective Soldering
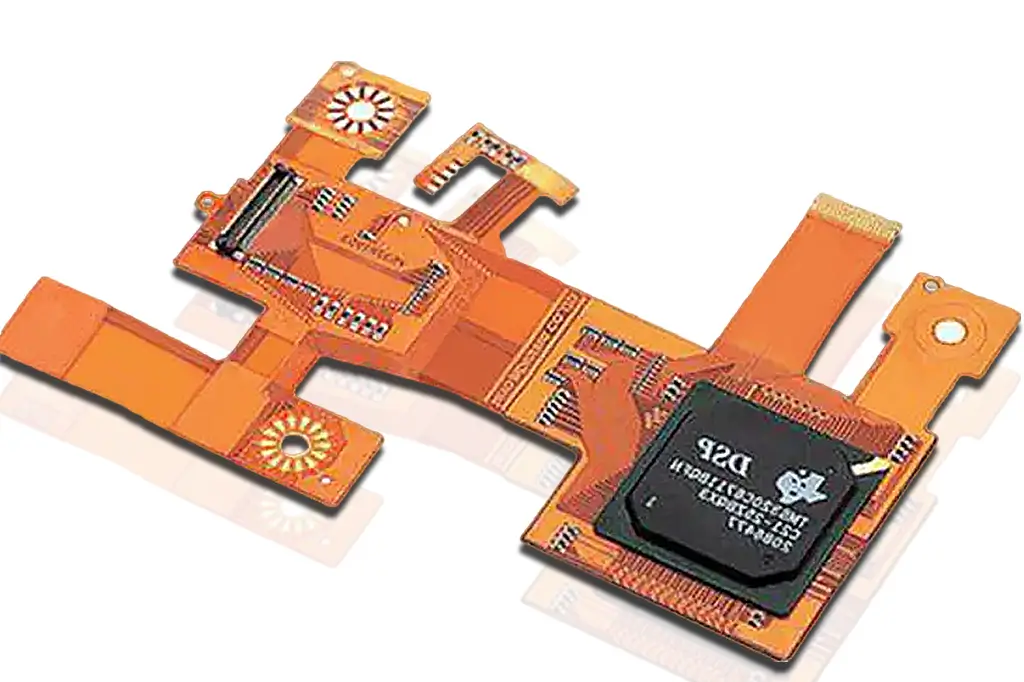
Considering of rigid-flex assembly
Rigid-flex PCBs are assembled similarly to rigid boards. However, there are a few differences.
Rigid-flex materials
Rigid-flex boards are fabricated using the same materials that hardboard and flexible boards are built with. The only difference is that they are built using no-flow prepreg. No flow prepreg is essential in rigid-flex manufacturing, as it flows up to the edge of the rigid-flex transition area without flowing out onto the flexible sections of the board.
Baking rigid-flex PCBs
Generally, the materials used in these boards (flex layers, coverlays, and bondplies) absorb water from their environment. The absorbed water will greatly expand during the thermal excursion of assembly and will damage the board. Hence, it is necessary to bake these boards prior to the assembly process.
Rigid-flex arrays
Generally, fabricators and assembly houses prefer to have rigid-flex circuits supplied in arrays. This holds the boards stable during assembly. Once the assembly process is completed, the boards are removed from the arrays .Always contact your manufacturer to know more about the array requirements.
Part Retention Within The Assembly Array
The most common solution for breakaways in rigid-flex PCBs are mouse bites – similar to standard rigid PCBs. For flexible circuit designs the common solutions are tabs. Tabs are the small uncut sections or the part outline.
V-scoring may also be used for rigid-flex designs. A post assembly cutting system will be required to finish the V-Score cut and allow the parts to be separated from the array. V-Scoring will leave the centrally located flex layers uncut. V-Score is generally not used on flex only designs as the cutting process leaves an undesirable rough edge finish. The flex design must also have FR4 stiffeners thick enough to accommodate the capabilities of the V-Score process.
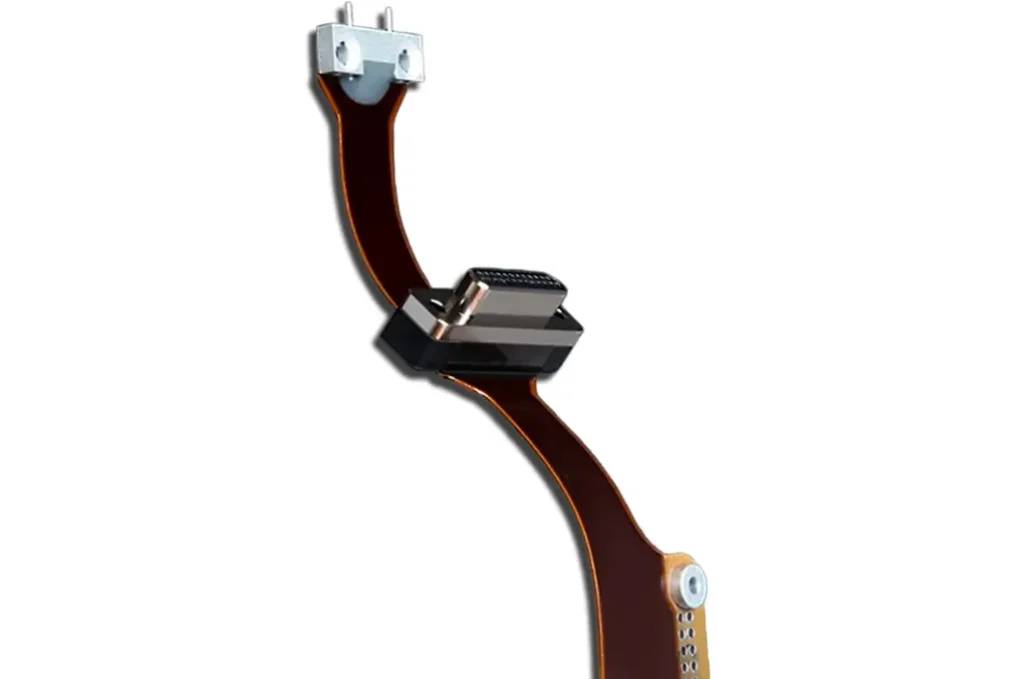
Rigid-flex assembly notes
Follow these guidelines:
- If components are placed close to the flex section, have stiffeners around the flex area.
- If the stiffeners are used for mechanical reasons, try to place components over the stiffener or rigid area.
- Flex circuits typically have SMT components on one only side of the board.
- Rigid-flex circuits are stiffened along most of their surface, with relatively small areas left unstiffened – the hinges or flexible arms.
- Apply stiffeners on the opposite side of SMT components and on the same side for through-hole components.
- The pre-bake cycle eliminates any moisture retained in the board and allows for improved assembly yields and reliability. However, if boards are assembled immediately after manufacturing, there is no need for pre-bake. Since Benchuang Electronics manufactures and assembles under one roof, we eliminate the need for pre-bake.
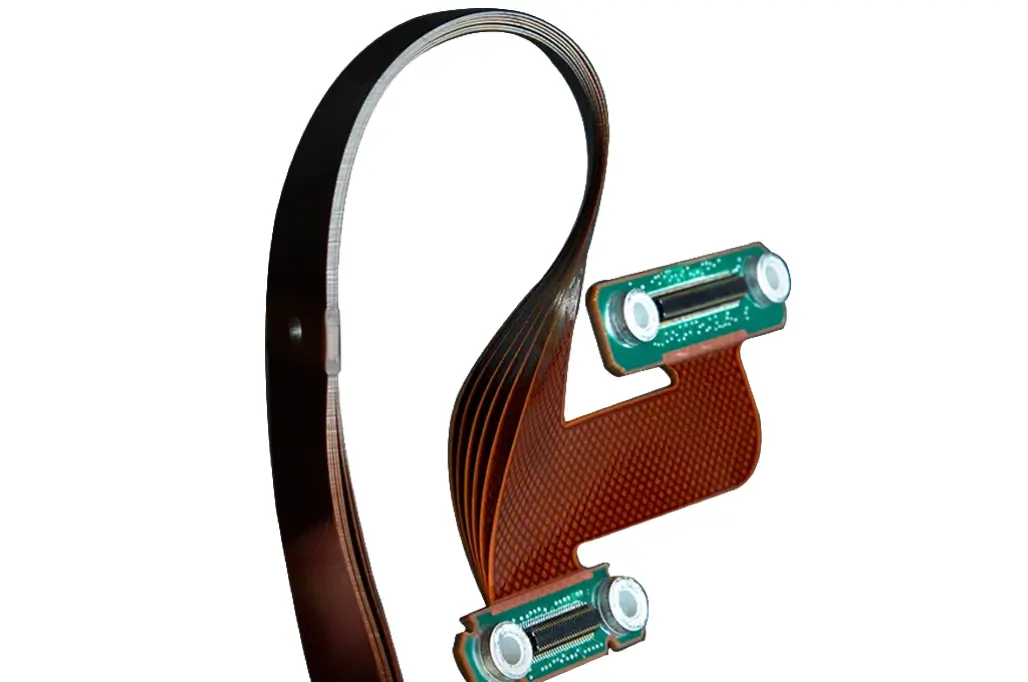
Rigid flex PCB Assembly Pre-Bake Specifications
Flexible Polyimide materials used in the fabrication of flexible and rigid-flex circuits are hydroscopic up to 2-3% by weight and as such require a thorough pre-bake to eliminate all moisture prior to any assembly process. This is an inherent property of the materials and is independent of the manufacturer and or the brand of polyimide materials used.
The industry accepted standard is to pre-bake all flex circuits immediately prior to assembly and without exceptions, even if the product has recently been received from the supplier in a vacuum sealed package. Baking the product prior to packaging does not eliminate the need for pre-baking prior to assembly.
Failure to remove all moisture is the primary cause of coverlay delamination, layer to layer delamination, and stiffener delamination. The root cause being the conversion of the entrapped moisture to steam at assembly re-flow temperatures. The expansion of the steam results in the delamination.
It is recommended that the flex PCB parts be pre-baked at 120°C. The duration of the pre-bake will vary depending upon the design of the specific parts. Layer count, stiffeners, and flex circuit construction are factors that will increase the pre-bake time required. Pre-bake times will vary from minimum of 2 hours up to 10 hours for high layer count flex circuit designs.
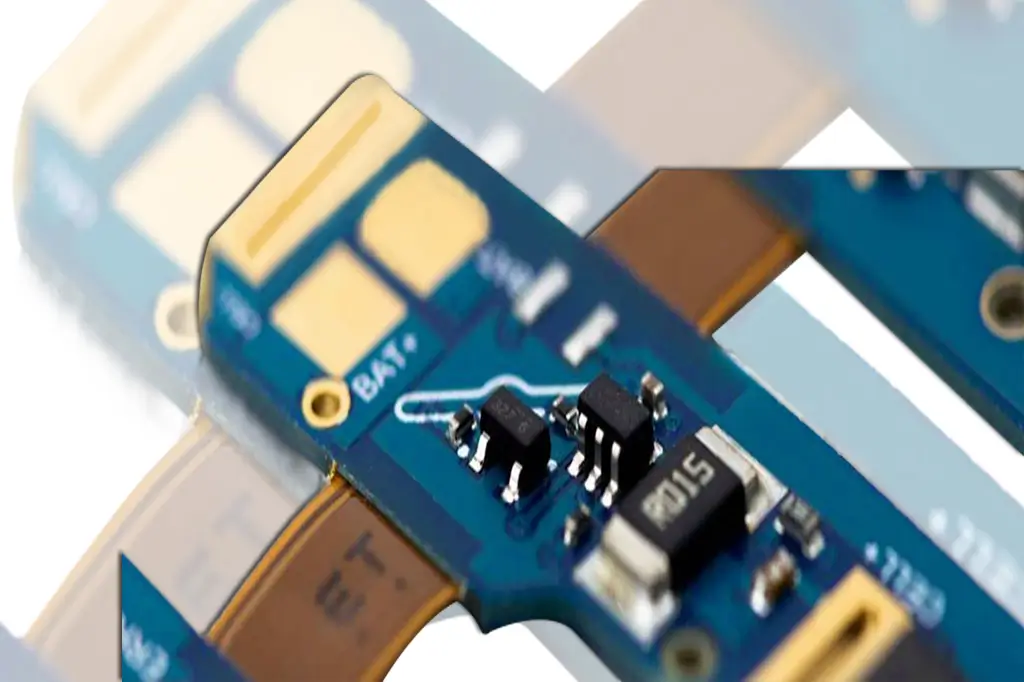
Rigid flex PCB Component Procurement
Benchuang Electronics offers full turn-key capabilities, which means we will take care of procuring all materials and components. A turn-key solution eliminates delays and allows for peace of mind knowing your PCB is in the hands of our expert engineers from start to finish. We also offer partial and consigned assembly services if you’d prefer to secure the components and materials yourself.
Rigid-flex boards have effectively reduced a product’s size without compromising the quality. They can solve contact and intense heat problems caused by harnesses and connectors, drastically improving the reliability of devices.
Get started with Printed Circuit Assembly
- Box build assembly
- Flex pcb assembly
- Rigid flex assembly
- SMT Assembly, BGA Assembly, Through hole Assembly, Mixed Assembly