- 部品実装、BGA実装、スルーホール実装、混合実装
- 基板組立またはボックスビルド組立サービス:部品実装または完全なエレクトロニクスアセンブリを提供
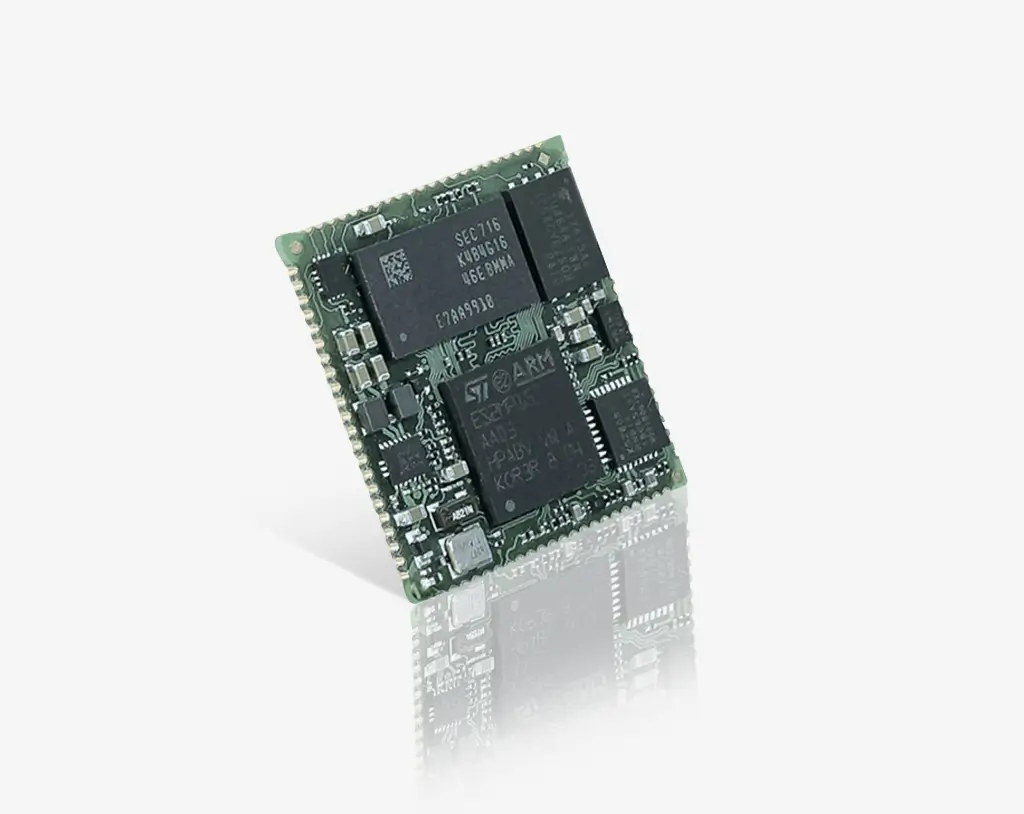
基板実装
Printed circuit board (PCB) assembly is the process of soldering electronic components onto bare boards. Electronic components installed on the bare board can be through-hole and/or surface mount (SMT). If the assembly has both, it is sometimes referred to as a high mix printed circuit board. PCB assembly is one segment of the electronic manufacturing process. Other segments can include cable/wire harness, mechanical/box builds, programming, and functional testing.
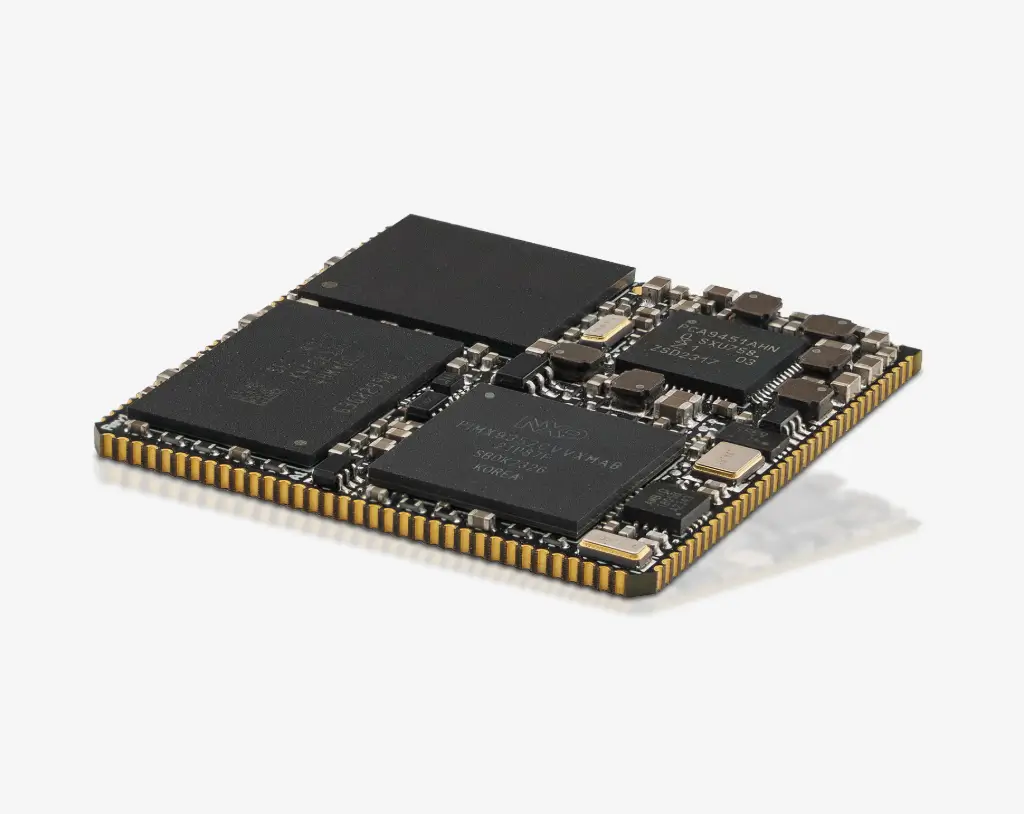
プリント基板実装内容
- SMT、スルーホール、混合アセンブリ対応
- 受動部品:最小01005サイズ対応
- ボールグリッドアレイ(BGA)
- 超微細ボールグリッドアレイ(uBGA)
- リードレスクアッドフラットパッケージ(QFN)
- クアッドフラットパッケージ(QFP)
- プラスチックリードチップキャリア(PLCC)
- SOICおよびパッケージオンパッケージ(PoP)
- 小型チップパッケージ(ピッチ0.2mm)
- ICプログラミング
- 機能テスト
PCB実装能力
PCB実装能力をダウンロード
最初から間違えないように、チェックリストとして使用するために設計ガイドラインをまとめました。
The file lists some of the fabrication features that are typically associated with pcb assembly. The feature limits listed are not comprehensive; Our experienced engineers have also worked with every type of PCB material, so they have the knowledge and expertise to provide recommendations and answer all of your pcb assembly questions. Most importantly, they know how to assist for manufacturability and the potential cost drivers of a project.
Parts Procurement | Full Turnkey, Partial Turnkey and Kitted/Consigned |
---|---|
Assmebly Types | Surface Mount (SMT), Thru-hole, Mixed Technology (SMT/Thru-hole),Single and double sided SMT/PTH , Large parts on both sides, BGA on both sides |
Largest PCB/Panel Size | 24 x 35ʺ |
Smallest PCB/Panel Size | 1.2ʺ wide |
Largest QFP Size/BGA Size | 75 mm x 87 mm |
BGA Pitch Range | From 0.25 mm to 3 mm |
Smallest QFP Pitch Range | From 0.25 mm to 3 mm |
Stencils | Laser cut stainless steel and Nano-coating |
Components | Passive components smallest size 01005,Fine pitch components smallest size 6 Mils pitch, Leadless chip carriers/ BGA, VFBGA, FPGA & DFN, Connectors and terminals |
Component packaging | Reels, Cut tape, Tube and Loose parts |
Inspection | X-ray analysis, AOI and Microscope to 20X |
Solder Type | Leaded and Lead-free/RoHS compliant |
Assembly surface mount connectors | Yes |
Wave Soldering | Yes |
Conformal Coating And Potting | Yes |
PCB Finish | SMOBC/HASL, Electrolytic gold , Electroless gold , Electroless silver, Immersion gold, Immersion tin and OSP |
Panelized PCB | Tab routed ,Breakaway tabs ,V-Scored and Routed+ V scored |
Design File Format | Gerber RS-274X, 274D, Eagle and AutoCAD’s DXF, DWG BOM (Bill of Materials) and Pick and Place file (XYRS) |
Other Services | Parts Management, IC Programming and Functional Testing |
もっと見る +
PCB実装の種類
- 表面実装(SMT)
- スルーホール
- 混合技術(SMT/スルーホール)
- 単面または両面実装
PCB基板実装のはんだタイプ
- リード入り
- リードフリー/RoHS準拠
- ノンクリーンおよび水洗浄フラックス
PCB実装部品タイプ
- 受動部品:最小01005サイズ対応
- ボールグリッドアレイ(BGA)
- クワッドフラットパッケージ ノーレッド(QFN)
- クアッドフラットパッケージ(QFP)
- 小型チップパッケージ(ピッチ0.2mm)
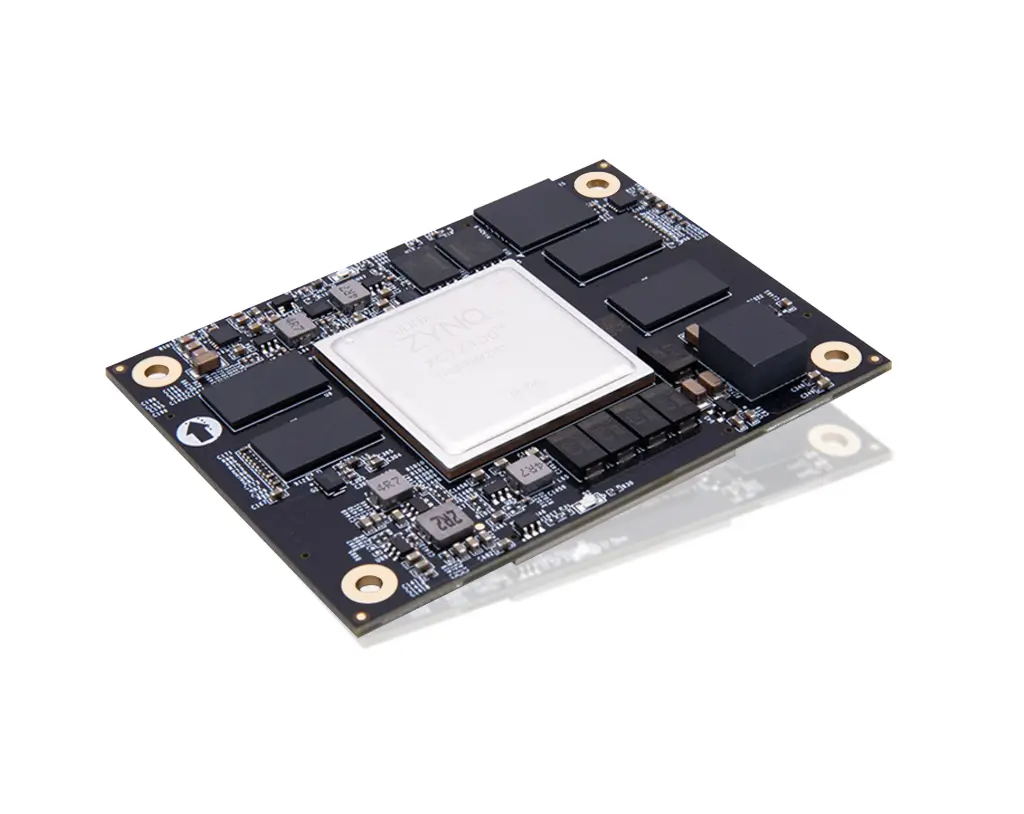
PCB実装の管理および検査
- AOIテスト(自動光学検査)
- 3D AOIテスト
- 3D SPIテスト
- X線検査
- インサーキットテスト
PCB実装製造機器
私たちは、品質がすべてのプロセスに組み込まれているという原則で運営しています。最初から最後まで、品質が最前面にあります。私たちは、コスト効果が高く、高品質なPCB実装サービスを提供し、優れたカスタマーサービスを確保することにコミットしています。
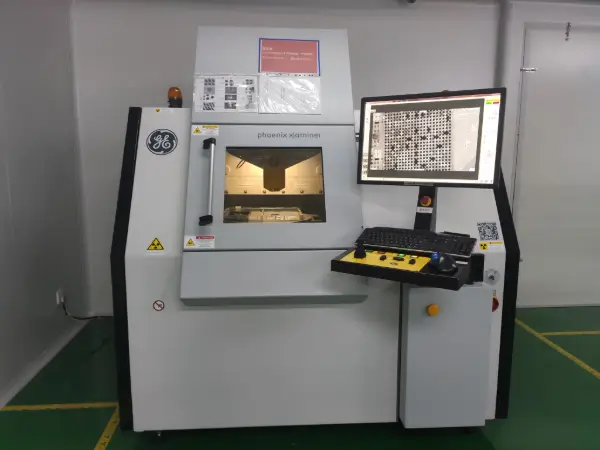
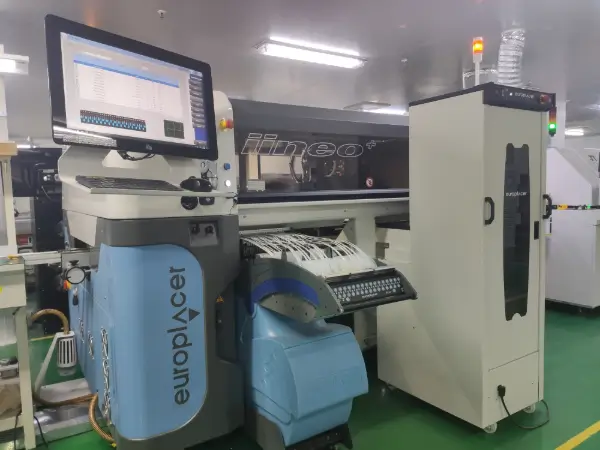
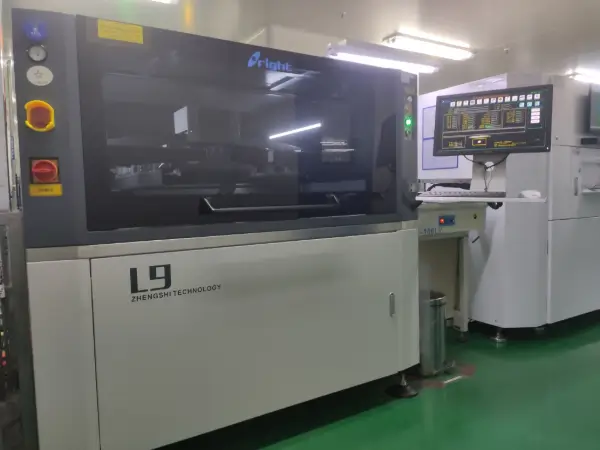
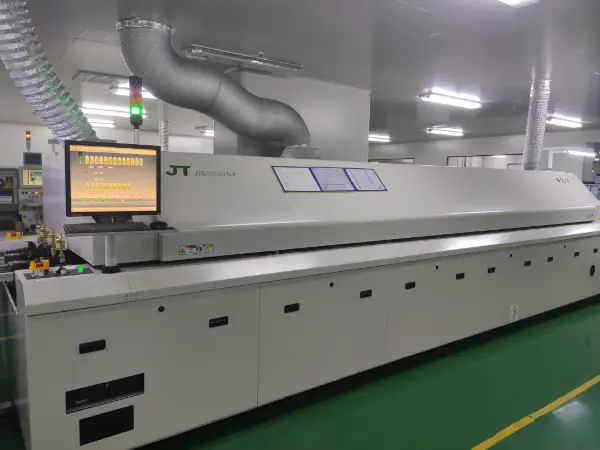
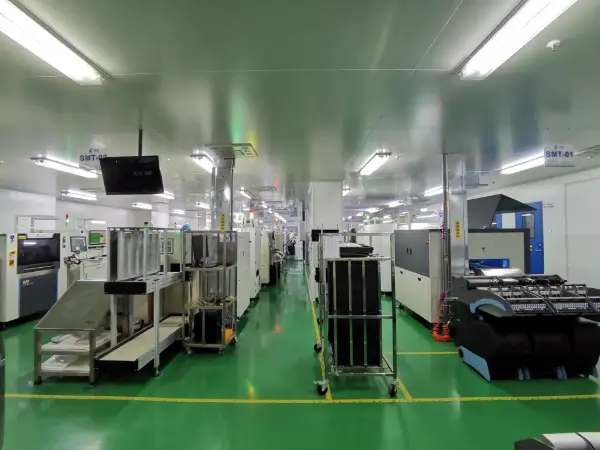
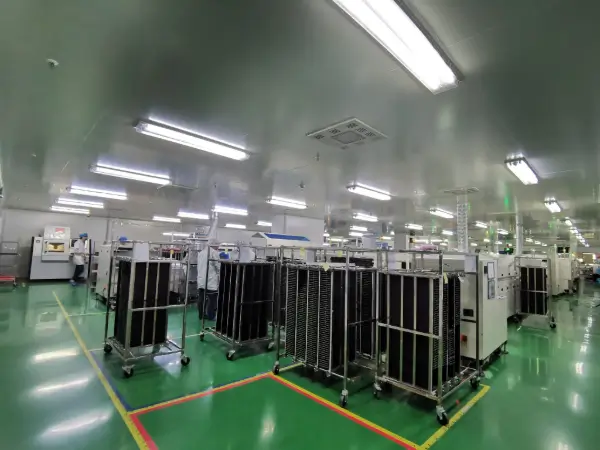
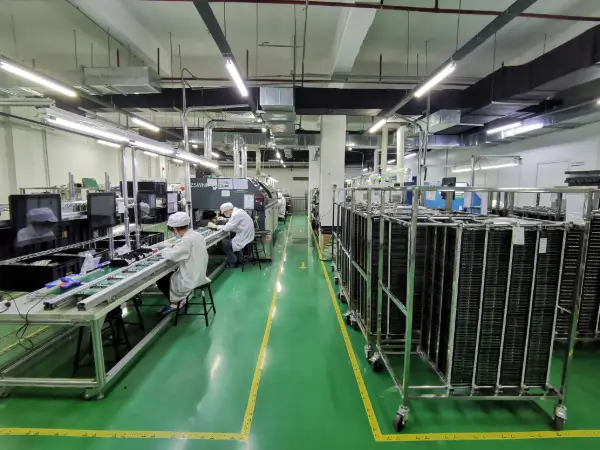
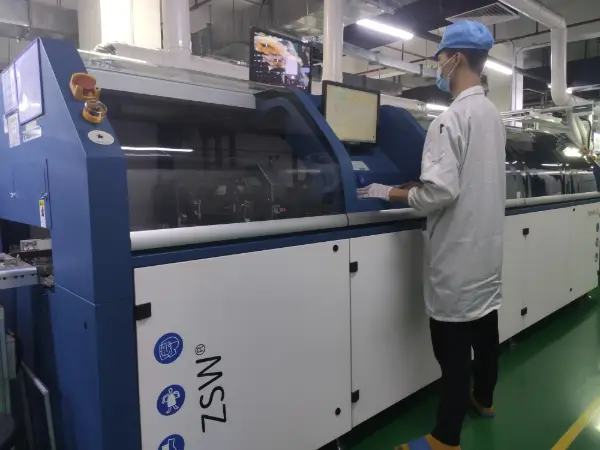
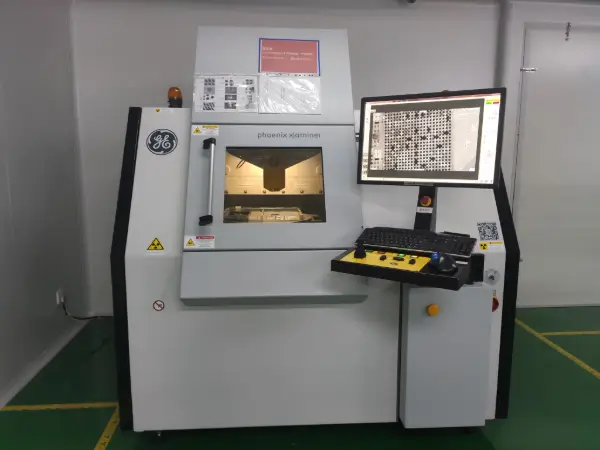
PCB実装ファイルの要件
ご注文には、以下のファイルを含めてください。1つのZIPファイルにまとめてご提出ください。
Gerberファイル
すべてのレイヤー(銅、はんだマスク、シルクスクリーン、はんだペーストなど)を含めてください。
センタロイドファイル
ピック・アンド・プレースファイルとも呼ばれ、部品の位置、回転、参照デザインatorsを含む必要があります。
BOMには以下を含める必要があります:
- 参照デザインators
- 各部品の数量
- メーカー部品番号
- 部品の説明
- 種類(SMT、スルーホール、細ピッチ、BGAなど)
- パッケージの説明(例:QFN32、SOIC、0805などのパッケージが非常に役立ちますが、必須ではありません)
プリント基板実装チェックリスト
ベンチュアンエレクトロニクスは、お客様にシームレスで正確な実装プロセスを体験していただきたいと考えています。作業が中断されないよう、以下のガイドラインに従ってください:
正確なデータ
エラーフリーな実装プロセスには正確なデータが必要です。各作業にはBOM(部品表)、ピック・アンド・プレースファイル(センタロイドファイルとも呼ばれます)、および一致するガーバーデータを含める必要があります。PCB上に部品を配置しない場合は、BOMに「DO NOT POPULATE(DNP)」列を追加してください。
適切なフットプリントの確認
部品は異なるパッケージで提供されることがあります。BOMに指定した部品がPCB上のフットプリントと一致することを確認してください。
部品の整理
部品は個別の袋またはトレーに分けて整理してください。各袋またはトレーには、製造業者名、部品番号、部品が使用される場所の参照デザインatorsを記載してください。必要に応じて、製造業者情報の代わりにディストリビューター名や部品番号を使用しても構いません。
複数の作業が1つの注文に含まれている場合
各作業の部品は別々にパッケージングしてください。各作業のために、別々のBOMおよびピック・アンド・プレースファイルを含めてください。
部品の数量
実装中に部品が紛失することを考慮して、予備の部品を含めてください。
小規模な生産(1〜25枚の基板)では、次のように予備部品が必要です:
- 0201〜0603サイズ:最小予備数量50個+必要数量
- 0805〜1206サイズ:最小予備数量25個+必要数量
- 大型部品は1〜2個の予備で問題ありません。
- すべてのSMT部品は連続したストリップまたはリールで提供することを推奨します。
- 大規模生産では、予備部品は割合で提供しても問題ありません。
未使用の部品は、組み立てられた基板をお客様に返送する際に返却いたします。
BOMとピック・アンド・プレースファイルの更新
設計変更がある場合は、BOM、ピック・アンド・プレースファイル、およびその他の関連書類にその変更を反映させることを忘れないでください。
極性のマーク
極性がある部品には、適切な向きを示すことを確認してください。ICのピン1には、向きが明示的でない場合、ドットまたは「1」という番号を付けてください。極性コンデンサやダイオードが正しくマークされていることを確認してください。
特別な指示
基板の実装に特別な手順が必要な場合、詳細な指示を提供してください。スケッチ、写真、PDFファイル、または図面を必要に応じて添付してください。
PCB実装プロセス
PCB製造プロセスでは、基板の構造が完全に確定し、その後にPCB実装プロセスが行われます。PCB製造中に、部品の取り付けに必要な特定の寸法を持つ穴が開けられ、実装段階ではこれらの穴に電子部品を確実かつ永続的に取り付けるための複数のアクションが順次行われます。
ステンシル準備
金属シートは、はんだペーストが後で充填される穴を除いて、プリント基板全体をカバーする必要があります。したがって、金属シートはPCBのデザインに従って処理され、シート内の開口部はPCBの穴の形状、幅、長さと一致します。この金属シートは「ステンシル」と呼ばれ、真鍮またはステンレス鋼で作られています。
ステンシル設計は非常に困難であり、ステンシルの形状の精度と均一な厚さが正確な実装を行うために不可欠です。ステンシルの典型的な厚さ範囲は0.0254mmから0.762mmです。金属シートの厚さは、特定のPCBで使用される電気部品の種類に依存し、各基板ごとに個別に決定されます。最小の過大または不足なサイズでも、後の実装工程で重大な問題を引き起こす可能性があります。大型の開口部では、ボーリングやブリッジングと呼ばれる現象が発生することがあります。これらの現象は、はんだを適用する際にPCB表面の一部や隣接する穴間全体にフィルムがかかることから生じます。その結果、PCBが完全に機能しなくなります。ステンシルのパラメータを選定した後、必要な組成と厚さで金属シートが金属工場から注文され、その厚さの均一性がX線ゲージを使用して検査され、製造工場に出荷されます。
化学エッチング
ステンシルの処理技術は少数ありますが、レーザー切断と化学エッチングが最も広く使用されています。化学エッチングプロセスでは、金属マスクと柔軟な金属マスクが両面からエッチングされます。まず、PCBのデザインがフィルムを使用して金属シートに転送されます。その後、シートが特定の酸溶液に浸され、開口部が形成されます。しかし、このプロセスの欠点は、酸がシートの深い部分に影響を与え、アンダーカットが生じることです。したがって、壁は追加で研磨され、はんだの適用に適した滑らかな表面が形成されます。壁を滑らかにする方法としては、電解研磨とニッケルメッキがあります。電解研磨は電気メッキの逆プロセスであり、電流を使用して過剰な金属部分を電解液に溶解させ、その後洗浄します。一方、ニッケルメッキでは、開口部の壁に追加の金属層が適用され、その直径が縮小されます。
レーザー切断PCB
PCB組立プロセス中にPCBをレーザー切断するために、専用のCNC機械が使用されます。レーザービームは、Gerberファイルに提供されたパターンに従って金属板を切断します。このファイルにはPCBの技術仕様がすべて含まれており、統合されたカスタムソフトウェアがそれらを読み取り、その後レーザーを切断プロセスに従って移動させます。金属結合は非常に強力であるため、レーザーのパラメータを微調整する必要があり、滑らかな金属端面を作成します。レーザー切断のプロセスにおいて重要なパラメータは以下の通りです:ビームスポットサイズ、ビーム焦点、切断速度、レーザー出力。レーザー出力は、常に十分である必要があり、ビームが金属板を貫通できるようにしなければなりません。PCB組立で最も一般的に使用されるビームスポットサイズは0.0254mmで、ほとんどの形状や開口サイズの切断に適しています。設定されたパラメータが正確であっても、開口部の壁を化学的エッチングプロセスと同様にエレクトロポリッシングやニッケルメッキによって追加的に滑らかにする必要があります。
はんだペースト印刷
PCB組立プロセス中に使用されるはんだペースト印刷には、特別なプリンターが使用されます。このタイプのプリンターは「スクイージーブレードプリンター」として広く知られています。スクイージーブレードは、はんだペーストをステンシルの表面とPCBの穴に押し込むために使用されます。これらのブレードは、生成する必要がある圧力範囲に応じて金属またはポリウレタンで作られることがあります。プリンターの内部視覚システムは、ステンシルを基板の上に垂直に位置合わせします。さらに、プリンターはステンシルの最高精度な位置決めのために、通常「グローバルフィデュシャルマーク」と呼ばれる3つのフィデュシャルを使用します。つまり、グローバルフィデュシャルマークは、印刷操作前および印刷中にX軸およびY軸方向のPCBのミスアライメントを即座に検出し、修正します。この方法により、スクイージーによる圧力で基板またはステンシルがずれることが完全に回避されます。
スクイージーの圧力は、特に注意して制御しなければならないパラメータです。圧力が高すぎると、ペーストが基板表面に広がり、いわゆるブリッジングやはんだペーストのブリーディング(流れ出し)を引き起こすなどの問題を引き起こします。ペーストは非常に粘性の高い懸濁液であるため、流れるためにはかなりの力が必要です。スクイージーの圧力は、ペーストとステンシルの間の高い摩擦力を克服するために十分でなければなりません。ペーストの移動が開始されると、ペーストは印刷可能な領域の幅を制御されたロールで移動し、すべてのステンシルの開口部を満たし、同時にスクイージーブレードによってステンシル表面の上から掃き取られます。スクイージーの標準的な作業圧力範囲は、印刷可能領域の1センチメートルあたり0.13kgから0.27kgの間です。動いているスクイージーは慣性を誘発し、その影響でペーストがPCBの穴に流れ込みます。スクイージーの速度は、連続的に監視しなければならないもう一つのパラメータです。スクイージーの圧力と速度は直接的に比例関係にあるため、速度は通常、1秒あたり75mm未満に保つ必要があります。速度が速すぎると、ブレードとステンシルの間の摩擦力が高くなり、時間が経つにつれてブレードの機械的故障を引き起こします。
はんだペースト印刷の3番目の重要なパラメータは、スクイージーとステンシルの間の角度です。通常設定される角度は60°です。これはペーストが重力によってPCBの穴に下方向に移動する最適な傾斜を形成するからです。角度が大きくなると、ステンシルの開口部からペーストがすくい取られてしまい、結果として十分な量のはんだペーストが得られません。逆に、角度が小さくなると、スクイージーが印刷を終えた後にステンシルにペーストの残留物が残ることになります。
通常の印刷操作は1枚のプリント基板につき15秒から45秒かかります。印刷はPCB組立の中で最も長い工程であり、その後、ステンシルがPCBから分離されるプロセスが続きます。印刷後の検査は、塗布されたはんだペースト層の品質保証と、次の工程である電子部品の表面実装に適しているかを確認するために重要です。品質保証は通常、プリンターの2D視覚システムまたは別の3Dシステムを用いて行われます。
ステンシルの分離と洗浄
印刷プロセスの終わりに、PCBはステンシルから分離されます。分離中に、はんだペーストはPCBの穴に残る必要があります。ステンシルの取り外し速度は、ステンシルが開口部からペーストを引き抜かないようにするために重要です。通常のステンシル移動速度は約3mm/秒です。速度が速すぎると、穴から完全にペーストが取り外せず、高いエッジが残ることになります。
数回の印刷操作後、ステンシルの洗浄により、ステンシルとPCBの間にペースト粒子が蓄積しないようにします。洗浄操作は2段階に分かれて行われます。最初に、ステンシルはイソプロピルアルコールなどの洗浄化学薬品で掃除されます。この段階では、ステンシルの下のエリアが清掃されます。次に、追加の真空洗浄が行われ、開口部が洗浄されてペーストがPCBの穴に流れ込むのを妨げないようにします。
印刷後のステンシルとスクイージーの状態の品質保証
機械部品の品質保証前に、自動洗浄システムがはんだペーストの残留物を完全に除去し、オペレーターが材料表面全体をよく見ることができるようにします。その後、オペレーターはステンシルとスクイージーの視覚検査を行い、ブレードとステンシルに機械的な欠陥がないかを確認します。もしスクイージーやステンシルに損傷が見つかった場合、信頼性の高い効率的な印刷プロセスを提供するために、欠陥部品を交換する必要があります。
基板実装におけるはんだペーストの成分、特性、および保管
成分
はんだペーストは、金属はんだ粒子がフラックス内に分散した懸濁液を表します。金属はんだはさまざまな元素から作られますが、最も一般的な成分は99.7%のスズと0.3%の銅です。金属粒子は球形をしており、その大きさはIPC J-STD 005に規定された種類基準に従って異なります。以前は鉛がよく使用されていましたが、現在は国際的な環境保護規制により、その使用は廃止されています。鉛は人体と環境に非常に危険な要素を含んでいるためです。一方、フラックスは接着剤として機能し、金属球を結びつけ、電子部品が基板のパッドに取り付けられることを可能にします。フラックスは非常に粘度が高く、金属粒子を一緒に保持し、酸化や腐食を防ぐために60~80%の活性成分を含んでいます。フラックス内の活性成分が高いため、金属酸化物の形成を防ぎます。
さらに、フラックスは、穴に印刷されたはんだペーストを用いてスルーホールピン部品をはんだ付けすることを可能にします。重量比で、混合はんだペーストは一般的に90%が金属で構成されています。ただし、フラックスの非金属成分は密度が低いため、ペーストの体積の最大半分を占めることがあります。
特性
はんだペーストは、非ニュートン流体、より正確には擬似塑性流体です。これは、適用される圧力が特定の値に達すると、流動抵抗が著しく低下することを意味します。この擬似塑性挙動は、はんだペーストが印刷時に成功するための重要な特性です。つまり、流動抵抗が大きく変化することにより、ペーストは印刷ストローク中にステンシルの穴の内外に流れますが、印刷ストロークが終了した時点で基板の穴内に残り、滑り落ちることはありません。
粘度は、流体が流れるのに対する抵抗を決定する物理的特性です。フラックスが含む化合物のほかに、金属とフラックスの比率が流動抵抗に最も大きな影響を与えます。金属化合物が増加すると、はんだペーストの粘度は大幅に増加します。印刷作業中、刃とステンシルの間の薄いはんだ膜は顕著な温度上昇に直面し、適用された圧力から生じる摩擦力が原因でペーストの粘度が減少します。
はんだペーストの保管
はんだペーストの適切な保管は、PCB実装の最高性能に必要な特性を維持するために不可欠です。はんだペーストは、金属が酸素や湿気と反応しないように、気密または密封された容器に保管する必要があります。球形金属粒子の大きな表面積により、金属は腐食しやすく、これが電子部品との結合強度を低下させます。また、温度も制御する必要があります。保管温度は8℃以下で、1℃が下限温度であり、フラックスに含まれる液体成分が凍結するのを防ぐためです。制御された保管条件により、金属粒子の酸化速度が低下し、熱感受性のあるフラックス活性成分の劣化速度も減少します。
電子部品の取り付け
はんだペーストが基板表面に適用された後、電子部品の取り付けは、いわゆる「ピックアンドプレース機」を使用して行われます。ピックアンドプレース機を稼働させる前に、その操作アルゴリズムは、部品表と部品配置リストをMycronic Mycenterワークステーションにアップロードすることによってプログラムされます。プログラミング後、オペレーターはピックアンドプレース機に必要な電子部品を供給します。これで、このロボット装置は稼働する準備が整います。操作中、部品の配置精度がPCB実装プロセスの品質を反映する重要なパラメータとなります。スクイージーブレードプリンターと同様に、ピックアンドプレース機は、パネルを位置決めして方向を決定するために3つのフィデューシャルポイントを使用します。フィデューシャルは、各基板の銅層にエッチングされた光学ターゲットです。
すべての部品にはバーコードが付けられ、機械はこれを認識します。ソフトウェアは部品の位置情報を基板に送信します。部品の識別と配置に加えて、装置は部品の寸法や設置に必要な回転角度を検出します。また、この機械は部品を取り扱う際に容量、抵抗、インダクタンスを測定して品質保証を行います。設計されたパラメータと測定されたパラメータに不一致が検出された場合、機械は即座にその部品を取り除きます。
キュアリングオーブンでのはんだ付け
一度基板表面に配置された電子部品は、はんだペーストによって永久に固定される必要があります。これは、はんだペーストがまず溶け、その後固まることによって実現します。硬化中、はんだ内の原子の空間的な配列が変化し、はんだの物理的特性の転換が、はんだジョイントの高い引張強度を引き起こします。溶解プロセスはキュアリングオーブン内で行われ、基板はコンベアベルトを通じてオーブンを移動します。加熱された空気は、コンベアベルトの動きに対向する方向に流れ、250℃から480℃の間で基板を効率的に対流加熱します。ペーストの設定温度が迅速に達成されるため、キュアリングプロセスは短期間で終了し、その後硬化プロセスが行われます。硬化プロセスもオーブン内で行われ、溶けたはんだが冷却され、最終的に硬化します。
検査および機能テスト
PCB組立後、オペレーターは基板がすべて正しく配置されているかを目視で検査します。目視検査後、基板は電源に接続され、機能テストが行われます。このテストでは、PCBが動作する正常な条件がシミュレートされ、欠陥が検出されない場合、基板は出荷準備完了となります。
コンフォーマルコーティング
コンフォーマルコーティングは、部品をさまざまな環境的影響(例えば湿気など)から保護する重要な工程です。
コンフォーマルコーティングは、基板上に塗布され、汚染物質とPCBとの間にバリアを作ります。また、基板内でのクロストーク、リーク電流、電気化学的移動を減少させる絶縁層を形成します。コーティング材料はアクリル、ポリウレタン、シリコン、エポキシ、または樹脂の組み合わせで構成されており、環境的および電気的保護を提供します。
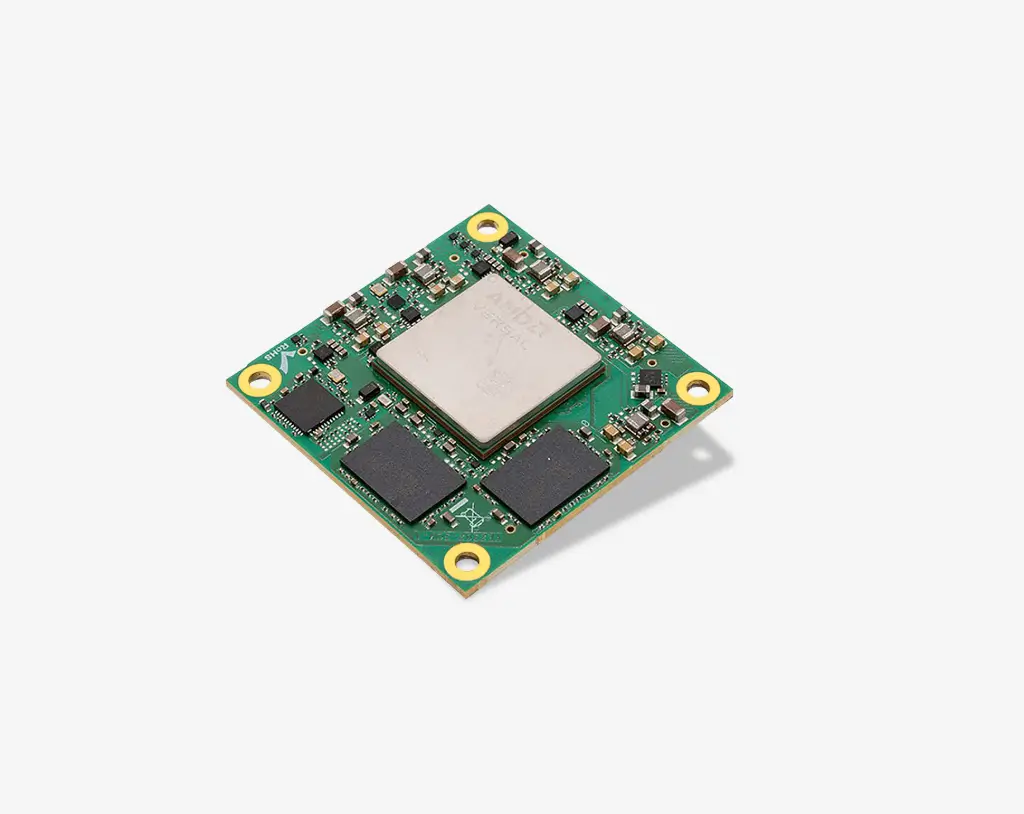
高品質なPCB実装
PCB実装プロセスは、基板製造後に行われ、基板構造がクライアントの要求に基づいて完全に形成されます。PCB実装プロセスは、ステンシル準備とはんだペースト印刷から始まり、SMD部品の配置、キュアリングオーブンでの接続形成、最終的な基板機能検査までをカバーします。ステンシル準備後、はんだペースト印刷が行われます。この段階では、電子部品を取り付けるための小さな開口部を非常に高精度で充填する必要があります。精度が低いと、ブリッジングなどの重大な問題が発生する可能性があります。ブリッジングは微小なサイズで、肉眼では確認できません。このため、最新の検査機器を使用しなければ、検出が難しくなります。それでも、ブリッジングはPCB実装プロセスで最も一般的な問題であり、ショート回路や部品の焼損を引き起こす原因となります。したがって、ベンチュアン電子では最新のはんだペースト印刷技術を活用し、組立ラインの終わりで各基板が適切に動作することを保証しています。
プリント基板組立を始める
- 電子部品組み立て
- 電子部品組み立て
- フレキシブル基板実装
- 部品実装、BGA実装、スルーホール実装、混合実装