- ブラインドビア、バリードビア、ウルトラHDIプリント基板
- 高周波低損失基板材料
- 低損失高速基板材料
- R-5775, R-5785, R-5795, TU-872 SLK , TU-872 SLK SP, TU 933+, I-Tera MT40, Astra MT77, Tachyon 100G 材料
- EM-888, EM-888(S), EM-888(K), EM-526, EM-528, EM-528K, IT-968, IT-968 SE, IT-988G, IT-988G SE 材料
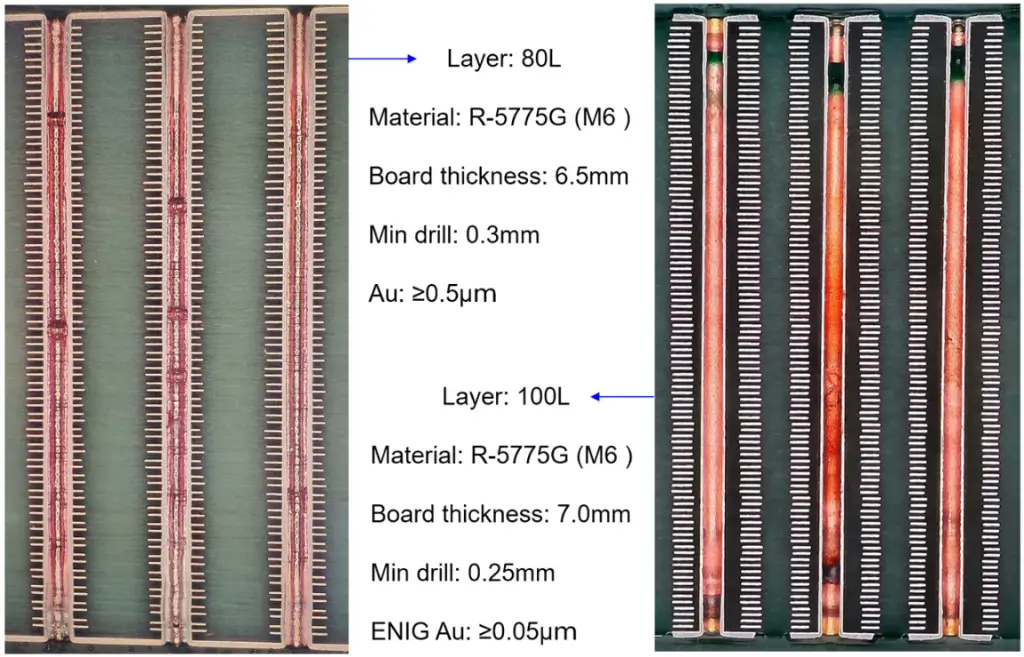
多層プリント基板
多層プリント基板は、3層以上の導電性銅層で構成される基板です。導電箔は多層回路基板の各層として配置されます。異なる内層はコア上でペアとして処理され、絶縁層としてプリプレグを使用して結合されます。その後、各層は配置され、基板の両面が使用可能となります。これにより、基板の内部に追加の配線や電気的接続を持ちながら、部品を搭載することができます。多層基板の異なる層間の電気的接続には、ビアが使用されます。
多層プリント基板は、以下のような多くの製品で使用されています:
· コンピュータ
· 医療機器
· 車載システム
· GPSおよび衛星システム
· 産業用制御システム
多層プリント基板の応用
ルーター/スイッチ基板
これらはLANとLAN、またはLANとWANを接続するためのネットワーク機器です。ルーターは主に外部通信ネットワークを担当し、複数のネットワーク間で適切な通信を確保するためのガイド役を果たします。一方、スイッチは独立したネットワークを担当し、通信経路上に複数のパケットが混雑している場合でも、定格通信容量を保証することで通信量が増加しても遅延なく入力速度を確保する機器です。
バックプレーンPCB
バックプレーンPCBは、ルーターとスイッチを接続する役割を果たす回路基板です。実際の大型バックプレーンに複数のルーター/スイッチや他のデバイスが差し込みスロットの形で搭載され、機器間でデータを転送するための経路を構築します。
バックプレーン(または「バックパネル」)は、通常のPCBよりも層数が多く、20層から40層以上になることが一般的です。また、サイズが大きく、厚みがあり、高速コネクタ用の圧入ホールが並んでいます。これらのコネクタにより、ドータカードやラインカードを簡単に差し替えたり交換したりすることが可能です。バックプレーンはパッシブ型とアクティブ型に分けられ、パッシブ型はオンボードの処理装置やメモリデバイスを持ちません。一部のケースでは、ラインカードが両面から差し込まれる場合があり、この場合の基板は「ミッドプレーン」と呼ばれます。
バックプレーンは非常に高速なデータ転送(>100GHz以上)に対応する必要があります。データ転送の信頼性は非常に重要であり、パケット損失がゼロであることが求められます。そのため、バックプレーンシステムでは信号の整合性(SI)が極めて重要です。
バックプレーンに使用されるベース材料は、通常、非常に低損失で、低DkガラスやHVLP銅箔が使用されることがあります。製造パネル上での画像の回転やジグザグ配線の使用により、織り目効果(ウィーブエフェクト)やスキューを最小限に抑える設計が行われます。
バックドリリング
バックドリリングは、スルーホール(PTH)の未使用部分(スタブ)を除去するために使用されます。スタブは信号反射を引き起こし、信号整合性(SI)を劣化させる原因となります。当社の最新バックドリルシステムは、パネルマッピング機能を備えており、深さの一貫性と再現性を確保します。
ベンチュアン電子では、両面からのバックドリリングをさまざまな深さで実施することが可能です。また、ブラインドビアや埋め込みビアを使用することで、ビアバレルの長さを最小化し、信号整合性を向上させることができます。
ベンチュアン電子は、以下の機能を含むバックプレーン組立のクイックターンおよび量産対応を提供します:
· UL®認証対応のハイブリッド構造(FR4および低損失積層材の統合)
· ブラインドビアおよび埋め込みビア
· スルーホール信号整合性の最適化
· 埋め込みキャパシタンス®
· 厚膜抵抗器
· RoHS準拠の表面仕上げ
サーバー/ストレージ用PCB
大容量データを保存・運用するためのハイエンドサーバー/ストレージ用PCB
近年、IT業界の急速な発展に伴い、ビッグデータの効率的な保守・管理の重要性とニーズがますます高まっています。
ベンチュアン電子は、超多層PCBに関する先進技術を基盤に、中国大陸地域のホワイトボックスサーバーマーケットに参入しました。当社は、著名なグローバル顧客を確保し、市場をリードしています。
スーパーコンピュータ(HPC)用PCB
超高速演算処理を行うスーパーコンピュータ用PCB
HPC(高性能コンピューティング、High-Performance Computing)は、国内ではスーパーコンピュータと呼ばれることが多く、主に研究機関、中国気象局、大手企業などが膨大なデータの迅速な演算処理のために利用しています。この市場規模は一般的に政府の投資規模によって左右されるため、需要の大きな変動性と技術の急速な変化を特徴としています。
航空宇宙用PCB
航空宇宙産業は、供給業者に対して非常に厳しい基準を課しています。その理由は明白で、他のどの業界よりも成功の期待値が高く、失敗がもたらす影響も甚大だからです。航空宇宙における取り組みに必要な機器は、非常に高度な技術と信頼性を求められますが、航空宇宙用PCBの信頼性もその一部に含まれます。
すべての航空宇宙システムの鍵となるプリント基板(PCB)の設計と性能は、完璧でなければなりません。この必要な品質を確保するため、航空宇宙産業の供給業者はAS9100規格を満たす必要があります。この規格は、品質システムに関するISO9001国際基準に加えて、さらに厳しい措置を課しており、関係者全員に対して強固な保護層を提供します。
航空宇宙産業では、手頃なコストでより高い技術性能が求められるニーズが増加しています。ベンチュアン電子は、この業界で要求される高性能、信頼性、極限環境への耐性に対応するため、製造設備と製造技術の両面で投資を行っています。
航空宇宙用PCBには、以下のような要件が含まれる場合があります:
· 5年以上(場合によっては15年以上)の使用寿命が期待されること
· 極限の条件下での性能が求められること:温度、湿度、振動、衝撃の過酷な条件や、塩水スプレー、飛砂や粉塵、太陽放射などの敵対的な環境条件での耐性。
プローブカード
プローブカードは、半導体ウェハ上の各チップの品質および欠陥を判定するため、メインテストシステムとプローブステーション(ウェハ自動供給装置)をウェハに接続する基板です。これは、ウェハ上の個々の半導体の電気的特性を検査するインターフェースデバイスであり、半導体の前工程に使用されます。
プローブカードは、チップとテスト機器間の動作を検査するための接続デバイスです。ウェハ上の半導体がパッケージング工程に進む前に、プローブカードがデバイスアンダーテスト(DUT)の不良を確認します。
ロードボード
ロードボードは、半導体後工程パッケージ(IC)の電気的特性、機能、性能をテストするためのインターフェースデバイスに使用されます。
ロードボードは、半導体産業のIC生産において、さまざまな種類のICテストを実施するために使用されます。信号または電気特性の伝送を通じて、ロードボードはICと自動テスト装置(ATE)間のインターフェースとしての役割を果たします。
バーンインボード
バーンインボードは、短寿命半導体を早期に検出するために使用される高温対応PCBです。高温および高電圧の極限ストレスを加え、デバイスを搭載してバーンイン試験を実施します。
当社のプリント基板製造能力は、さまざまな密度、層数、材料、プロセス、仕上げに対応しています。2層基板は最短で当日、多層基板プロジェクトは最短で24時間という迅速な対応で知られています。
当社は、バーンインボード(BIB)の設計および製造における市場リーダーです。バーンインボードは、バーンインプロセスで治具として機能するプリント基板であり、ASICの信頼性試験プロセスの一環として使用されます。この試験中、プリント基板のコンポーネントはストレスを加えられ、不良を検出します。バーンインボードには、テスト対象のASICを収容するソケットが含まれ、高温環境での試験に耐えるよう設計されています。当社の専門家は、すべてのアクティブ/パッシブコンポーネントおよびコネクタが高温要件を満たしていることを確認し、すべての材料および部品が高温およびオーブンエイジング要件に準拠していることを保証します。
材料選定から部品選定に至るまで、試験の性質に基づいて慎重に仕様を満たすものを選択します。HTOL、LTOL、PTC、HAST、および85/85など、さまざまな試験条件に対応するボードを提供します。各バーンインボードは、バーンインボード設計の専門エンジニアによって設計され、顧客のアプリケーション要件および仕様に合わせてカスタマイズ可能です。
ユニバーサル基板設計およびカスタムプリント基板設計のどちらにも迅速に対応可能です。すべてのサイズ、さまざまな複雑性、BGA、LGA、QFP、DIP、カスタムソケット、多層設計において、試作から量産まで対応しています。
125℃から250℃のピーク温度範囲に対応したバーンインボードを製造しています。テスト温度に応じて、高Tg FR4または特殊ポリイミド材料を使用します。
ADAS RFレーダー用PCB
自動車用レーダーPCBは、自動車通信の新時代を切り開きます。
ADAS(先進運転支援システム)は、77~79GHzの高周波アンテナがPCB上に形成されており、自動車の距離、位置、情報を送受信する機能を持つ製品です。
現在、自動車1台あたり2~6個程度搭載されていますが、将来的には自動運転の普及とともに、1台あたり最大20個程度まで需要が増加すると予測されています。ベンチュアン電子は、超多層PCBに使用される特殊材料のノウハウを基に、グローバル顧客と共に製品開発に注力しています。
ベンチュアン電子は、OEMおよび一級自動車電子機器メーカーに対して、高度な技術と高信頼性を備えたプリント基板(PCB)の完全ライフサイクルに対応する戦略的サプライヤーです。当社は、以下のニーズを一括でサポートするワンストップソリューションを提供します:
· 地域ごとの試作および超短納期対応
· 大量生産対応
· ヘビーカッパーからRF/mmWave技術までの幅広い技術サポート
当社のエンジニアチームは、あらゆる自動車顧客のPCBニーズに対応します。
ベンチュアン電子は、先進運転支援システム(ADAS)、eモビリティ、高電流・高電圧・高熱負荷アプリケーションを伴う電動パワートレインシステム、そして接続性における高度なソリューションと専門技術の継続的な開発に取り組んでいます。
高周波基板
高周波プリント基板(RF PCB)は、100MHz以上の周波数で動作するプリント基板を指します。特に、2GHz以上の場合はマイクロ波PCBに分類されます。
高周波(RF)プリント基板は、非常に低い周波数から超高周波までの電波を使用するプロジェクトに一般的に使用されます。これには、携帯電話から軍用レーダーまで、通信信号を伴うすべてのアプリケーションが含まれます。
RFマイクロ波PCBは、高周波およびマイクロ波周波数帯域の信号を最小限の信号損失で処理し、最大限の信号整合性を確保するよう設計された特殊なプリント基板です。これらは、以下のようなさまざまな電子機器に使用されています:
· 無線通信システム
· 衛星通信システム
· レーダーシステム
· その他の高周波電子システム
RFマイクロ波PCBの設計と製造には、期待される性能を確保するための高度な知識と豊富な経験が必要です。これらの基板は、信号の整合性と低損失性能を重視するアプリケーションにおいて不可欠な役割を果たします。
多層プリント基板の製造
多層プリント基板の需要は増加の一途をたどっています。電子機器がより小型化、高速化、そして高性能化を求められる中、多層基板はますます普及しています。多層基板を製造する能力は、より高密度な回路基板の設計を可能にし、小型化を実現します。この利点は、両面基板では提供できない大きな特徴です。
多層プリント基板の製造能力
当社の多層プリント基板の設計ガイドラインをダウンロードしてください
最初から間違えないように、チェックリストとして使用するために設計ガイドラインをまとめました。
設計段階でのミスを防ぐため、チェックリストとして使用できる設計ガイドラインを作成しました。
このファイルには、多層基板に通常関連する製造特性が記載されています。ただし、記載されている仕様制限は網羅的ではありません。当社の経験豊富なエンジニアは、あらゆる種類のPCB材料を取り扱った経験があり、その知識と専門性に基づいてお客様に推奨事項を提供し、あらゆる多層基板に関する質問にお答えします。最も重要なことは、製造可能性の支援とプロジェクトの潜在的なコスト要因の特定に役立つことです。
Description | Production | Advanced |
---|---|---|
Inner Layer | ||
Min.Trace/Space | 1.5mils / 1.5mils | 1.2mils / 1.5mils |
Min. Copper Thickness | 1/3oz | 1/7 oz |
Max. Copper Thickness | 10oz | 30oz |
Min. Core Thickness | 2mils | 1.5mils |
Line/ pad to drill hole | 7mils | 6mils |
Line/ pad to board edge | 8mils | 7mils |
Line Tolerance | +/-10% | +/-10% |
Board Dimensions | ||
Max. Finish Board Size | 19”X26” | 20”X28” |
min. Finish Board Size | 0.2"X0.2" | 0.15"X0.15" |
Max. Board Thickness | 0.300"(+/-10%) | 0.350"(+/-8%) |
Min. Board Thickness | 0.007"(+/-10%) | 0.005"(+/-10%) |
Lamination | ||
Layer Count | 60L | 100L |
Layer to Layer Registration | +/-4mils | +/-2mils |
Drilling | ||
Min. Drill Size | 6mils | 5mils |
Min. Hole to Hole Pitch | 16mils(0.4mm) | 14mils(0.35mm) |
True position Tolerance | +/-3mils | +/-2mils |
Slot Diameter Tolerance | +/-3mils | +/-2mils |
Min gap from PTH to track inner layers | 7mils | 6mils |
Min. PTH edge to PTH edge space | 9mils | 8mils |
Plating | ||
Max. Aspect Ratio | 28:1 | 30:1 |
Cu Thickness in Through hole | 0.8-1.5 mils | 2 oz |
Plated hole size tolerance | +/-2mils | +/-1.5mils |
NPTH hole tolerance | +/-2mils | +/-1mils |
Min. Via in pad Fill hole size | 6mils | 4mils |
Via in pad Fill Material | Epoxy resin/Copper paste | Epoxy resin/Copper paste |
Outer Layer | ||
Min. Trace/Space | 2mils / 2mils | 1.5mils / 1.5mils |
Min. pad over drill size | 6mils | 5mils |
Max. Copper thickness | 12 oz | 30 oz |
Line/ pad to board edge | 8mils | 7mils |
Line Tolerance | +/-15% | +/-10% |
Metal Finish | ||
HASL | 50-1000u” | 50-1000u” |
HASL+Selective Hard gold | Yes | Yes |
OSP | 8-20u” | 8-20u” |
Selective ENIG+OSP | Yes | Yes |
ENIG(Nickel/Gold) | 80-200u”/2-9 u” | 250u”/ 10u” |
Immersion Silver | 6-18u” | 6-18u” |
Hard Gold for Tab | 10-80u” | 10-80u” |
Immersion Tin | 30u”min. | 30u” min. |
ENEPIG (Ni/Pd/Au) | 125u"/4u"/1u” min. | 150u"/8u"/2u” min. |
Soft Gold (Nickel/ Gold) | 200u”/ 20u”min. | 200u”/ 20u” |
Solder Mask | ||
S/M Thickness | 0.4mils min. | 2mils max. |
Solder dam width | 4mils | 3mils |
S/M registration tolerance | +/-2mils | +/-1.5mils |
S/M over line | 3.5mils | 2mils / 2mils |
Legend | ||
Min. Space to SMD pad | 6mils | 5mils |
Min. Stroke Width | 6mils | 5mils |
Min. Space to Copper pad | 6mils | 5mils |
Standard Color | White , Yellow, Black | N/A |
Electrical Testing | ||
Max. Test Points | 30000 Points | 30000 Points |
Smallest SMT Pitch | 16mils(0.4mm) | 12mils(0.3mm) |
Smallest BGA Pitch | 10mils(0.25mm) | 6mils(0.15mm) |
NC Rout | ||
Min. Rout to copper space | 8mils | 7mils |
Rout tolerance | +/-4mils | +/-3mils |
Scoring (V-cut) | ||
Conductor to center line | 15mils | 15mils |
X&Y Position Tolerance | +/-4mils | +/-3mils |
Score Anger | 30o/45o | 30o/45o |
Score Web | 10mils min. | 8mils min. |
Beveling | ||
bevel anger | 20-71o | 20-71o |
Bevel Dimensional Tolerance | +/-10mils | +/-10mils |
Impedance controll | ||
Impedance controll | +/-10% | +/-7% |
もっと見る +
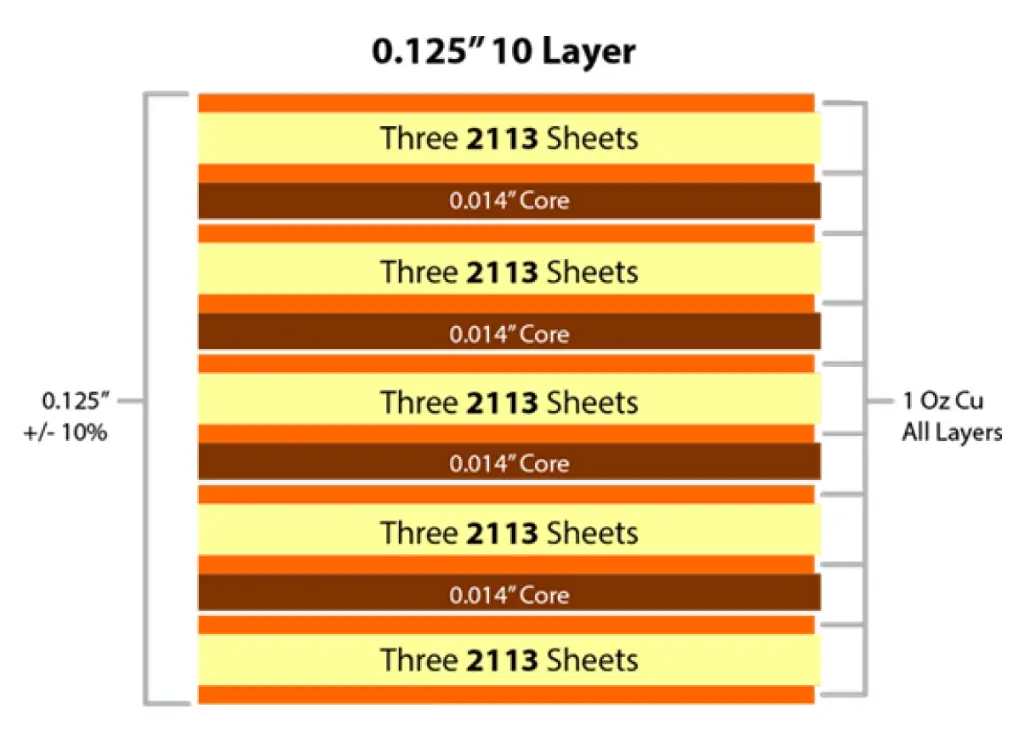
多層プリント基板の積層プロセス
積層プロセスに使用される材料には、内層コア、「プリプレグ」(エポキシ樹脂を含浸させたガラス織布)シート、銅箔シートが含まれます。各材料やコアには、積層時の位置合わせを行うための工具用穴が設けられています。4層基板の場合、最下層には銅箔シートが配置され、その上に所定枚数のプリプレグシート、内層コアが続きます。その上にさらにプリプレグが重ねられ、最後に最上層の銅箔シートが配置されます。このパネルの積層体は重い金属板の上に構築され、完成したら上部に金属板を追加して「ブック」が形成されます。このブックは、加熱式油圧プレスに移動されます。
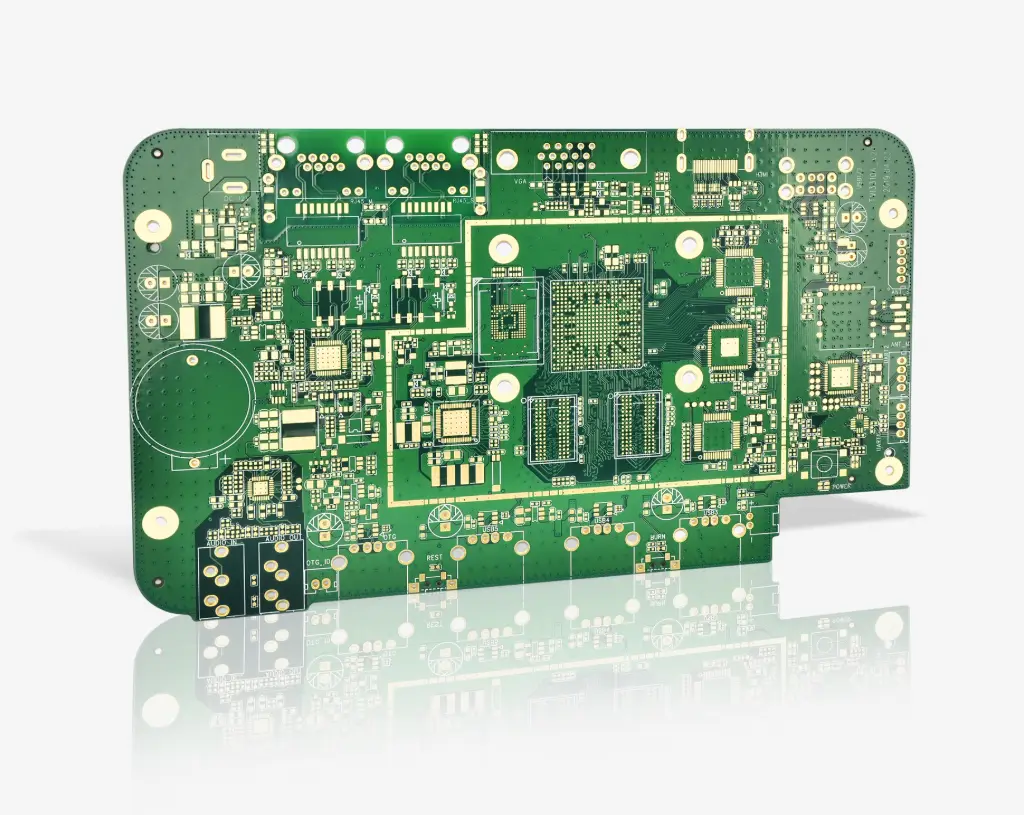
多層プリント基板のラップメッキ
ラップメッキとは、ドリル穴が銅でメッキされ、そのメッキが穴から基板上および表面に広がるプロセスを指します。このメッキは銅製であり、ビア構造の周囲やキャップメッキの下部を経由して表面に広がります。
電解穴メッキ厚にはさまざまなクラス仕様があります。IPC-6012規格(およびIPC-A-600検査規格)では、クラスI、クラスII、クラスIIIのカテゴリーに分かれています。
1. クラスI:厚さ仕様は、ユーザーとサプライヤー間の合意(AABUS)に基づきます。このクラス仕様は、ほとんどの製造施設ではあまり採用されていない選択肢です。
2. クラスII仕様では、ラップメッキが充填メッキされた穴を通じて連続し、PCBの表面にまで延長される必要があります。ビア構造およびスルーホールのラップメッキ厚は5μm(197μin)以上でなければなりません。また、平坦化、研磨、エッチングなどのプロセスによって銅材の厚みが減少する場合でも、ラップメッキが不足しないようにする必要があります。
3. クラスIII仕様はクラスII仕様と類似していますが、スルーホール、ブラインドビア、および2層以上の埋め込みビアのラップメッキ厚が12μm(472μin)未満にならないことが要求されます。埋め込みビアコアのメッキ厚は最低7μm(276μin)が必要であり、ブラインドビアおよび埋め込みマイクロビアのラップ厚は最低6μm(236μin)でなければなりません。
PCBのラップメッキには多くの課題が伴います。
· 膝部クラック:PCBの熱サイクル中にメッキが膨張することで、温度、PCBの層数、材料の熱膨張係数(CTE)に起因して、ラップメッキに応力クラックが発生する場合があります。
· バットジョイントの故障:熱サイクルによってバットジョイント部分が故障する可能性があります。
· 平坦化プロセスでの厚み管理:平坦化プロセス中にラップメッキの厚みが±0.3ミルの範囲で変動する場合があり、最低厚さ基準を満たすことが難しくなる場合があります。
多層プリント基板のコスト
多層プリント基板のデメリットを挙げるとすれば、単層基板や二層基板に比べて全体的にコストが高くなることです。しかし、多層基板を選択するメーカーは、そのコスト増を補うだけの多用途性と性能向上を重視しています。
層数が増えると、使用材料が多くなり、生産時間が長くなるためコストが上昇します。
高Tg FR-4やポリイミドなどの特殊材料はコストが高いですが、高性能基板には必要不可欠です。
生産量が多いほど、スケールメリットにより1枚あたりのコストを削減できます。
HDIやマイクロビアの使用などの高度な技術が必要な場合、コストが増加します。
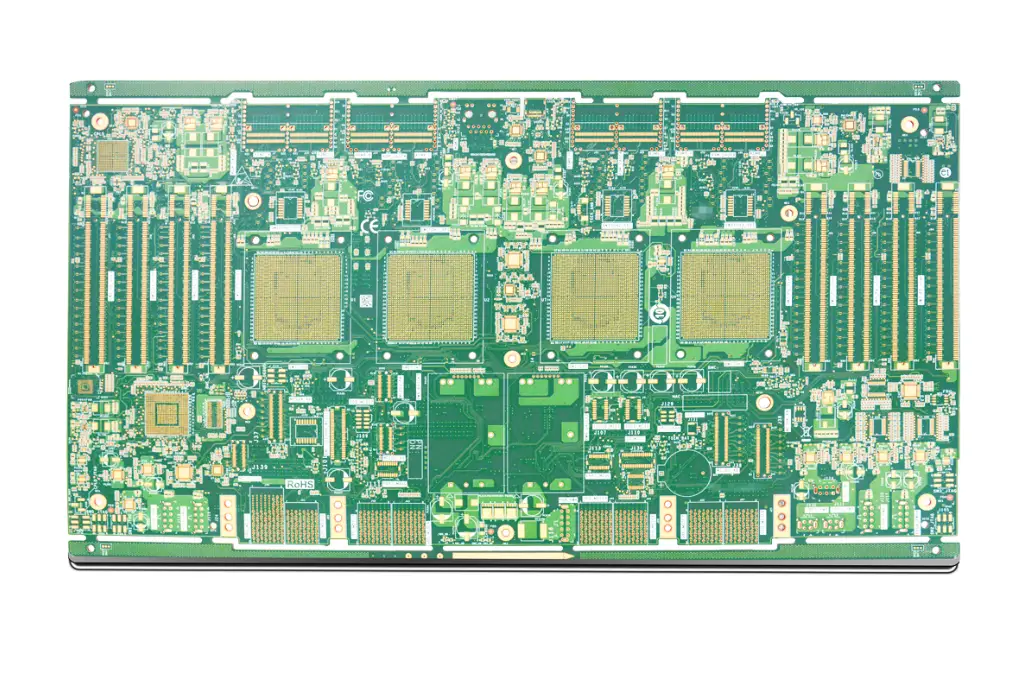
4層プリント基板
小型化された電子製品が普及する中、小型回路基板の需要が増加しています。そのため、多層回路基板が主流となりつつあります。4層PCBの積層構造はますます一般的になっています。ここでは、4層プリント基板について詳しく見ていきます。
4層の積層構造は、シンプルな設計の出発点として人気があります。コストを抑えつつ、高い製造適性を持つ4層設計は、今日の設計環境において、より高度で複雑な基板と並存しています。4層積層構造を決定する際には、配置するコンポーネントの数と必要な配線を分析することから始まります。
4層プリント基板の積層構造
4層積層構造には、レイヤーを配置する方法が少なくとも12種類以上ありますが、最も一般的な構造は3つに分類されます。これらの一般的な4層積層構造は、プレーン層が使用されることを考慮しており、これが4層積層構造を採用する主な理由の1つです。以下に、最も一般的な3つの4層積層構造のアプローチを示します。
4層基板の積層構造の3つの選択肢
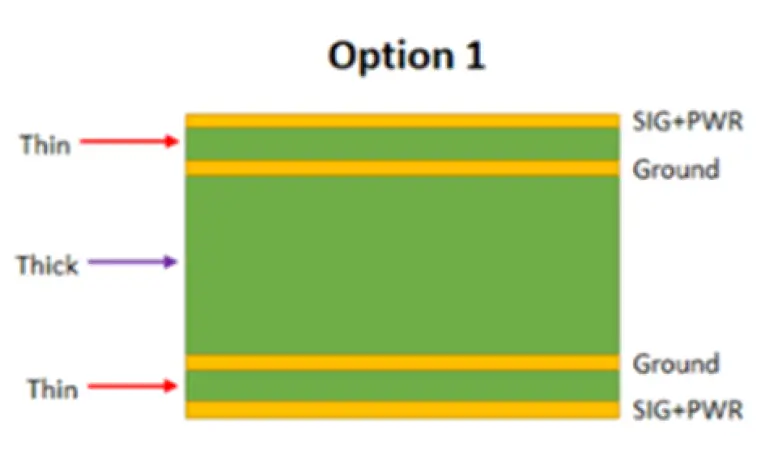
オプション1
SIG+PWR/GNDタイプの積層構造
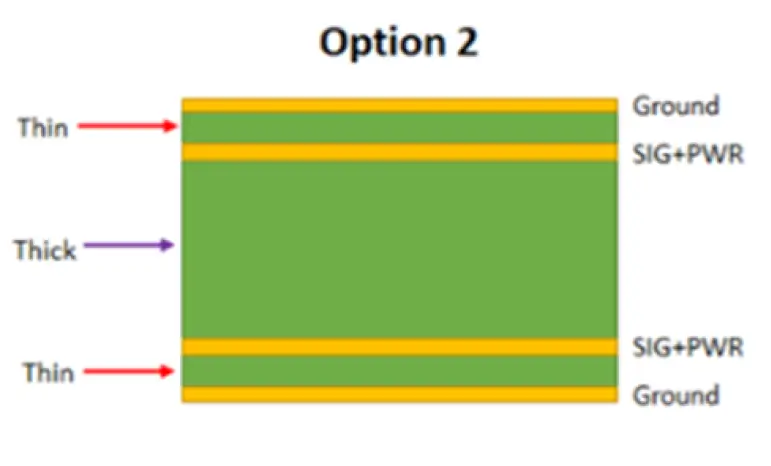
オプション2
SIG/GND/PWR/SIGタイプの積層構造
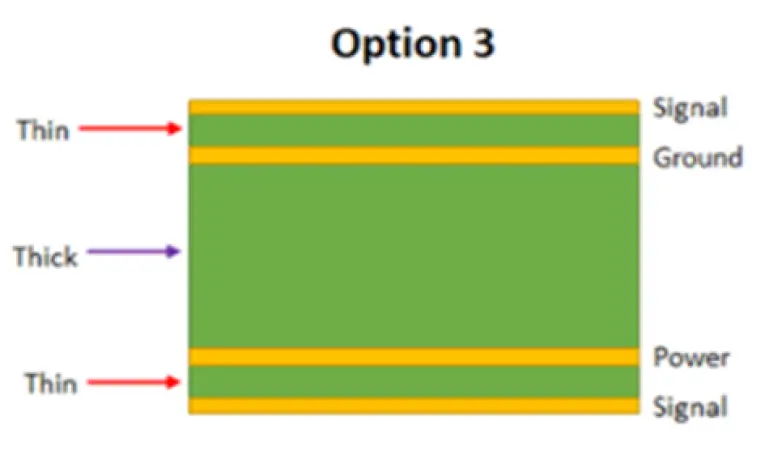
オプション3
SIG/GND/SIG + PWR/GNDタイプの積層構造
4層プリント基板の積層厚さ(コアおよびプリプレグの厚さ)
4層プリント基板には、2種類のコアおよびプリプレグの厚さがあります。標準厚さは1.6mm(約0.06インチ)ですが、1.2mm(約0.05インチ)も一般的に使用されます。
コアとプリプレグの違いについては、すでに公開されている記事で詳しく確認することができます。
1.6mm(約0.06インチ)厚のPCBの場合
コア材の厚さは1.2mm(約0.05インチ)で、プリプレグの厚さはそれぞれ0.2mm(約0.01インチ)です。
1.2mm(約0.05インチ)厚のPCBの場合
コア材の厚さは0.8mm(約0.03インチ)、コイル付きプリプレグの厚さが0.2mm(約0.01インチ)、銅付きプリプレグの厚さも0.2mm(約0.01インチ)です。
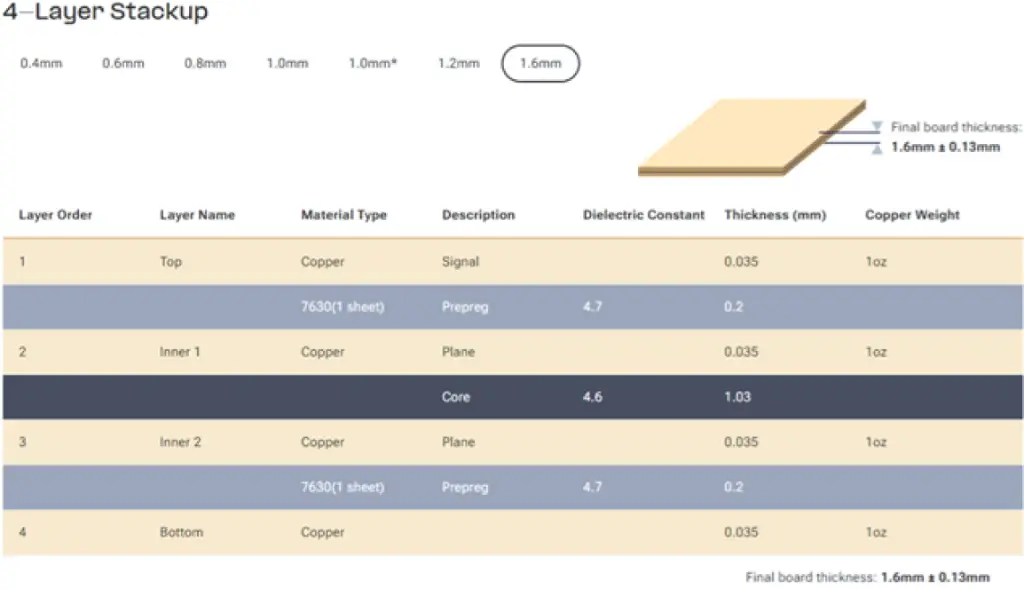
4層プリント基板の積層例
PCB製造工場では、4層プリント基板を含む多くの製造に対応する標準的な積層構造を使用しています。製造業者のエンジニアが使用する4層積層構造は、標準厚さ1.57mmであることが多いですが、他にも一般的な厚さとして1mmや2mmなどが利用可能です。設計に特定の材料要件がない場合、製造業者はその標準的な積層構造を使用します。
通常、標準的な積層構造は、以下のような表形式で指定されます。この表には、層の厚さと誘電率が最低限記載されており、Tg値(ガラス転移温度)の2つのオプションが提供される場合もあります。
多層プリント基板の製造プロセス
標準的なプリント基板というものは存在しません。各プリント基板(PCB)は、特定の製品に対応するユニークな機能を持っています。そのため、PCBの製造は複雑な多段階プロセスです。以下は、多層プリント基板を製造する際の主要な工程の概要です。
- PPE - 生産前エンジニアリング
- 材料準備
- 内層処理
- 内層エッチング
- 内層AOI(自動光学検査)
- 積層(ラミネーション)
- ドリリング(穴あけ)
- PTH - スルーホールメッキ
- パネルメッキ
- 外層イメージング
- パターンメッキ
- 外層エッチング
- 外層AOI(自動光学検査)
- ビアホールプラグ
- ソルダーレジスト(はんだマスク)
- 表面仕上げ
- プロファイル加工
- ET - 電気検査
- 最終検査
- 梱包
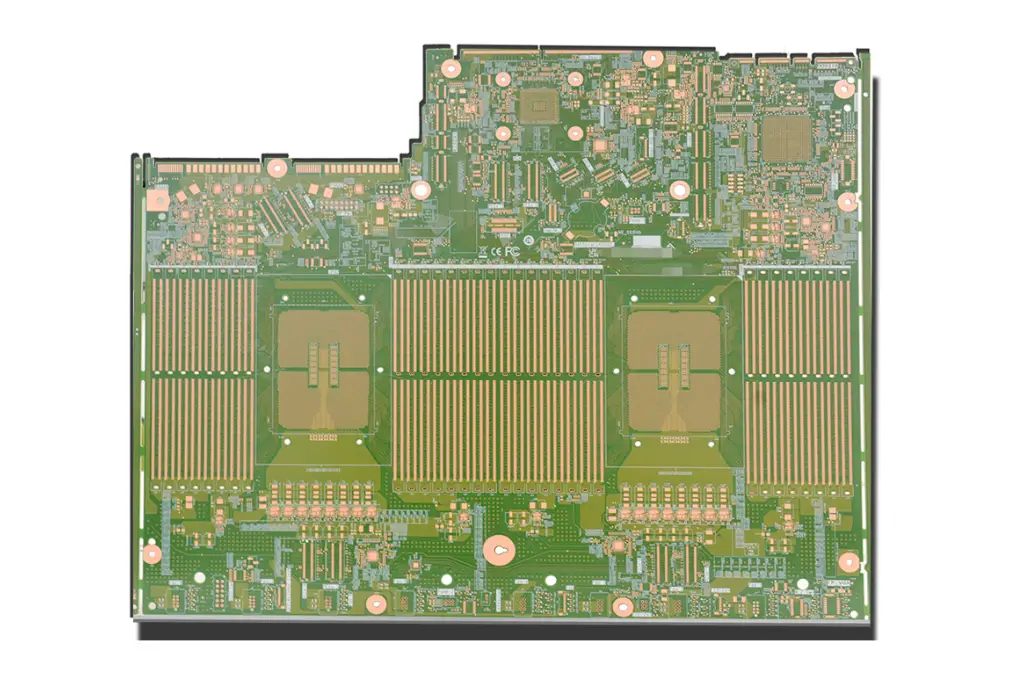
高品質な多層プリント基板の供給業者
多層プリント基板を製造するプロセスには、専門的な設備と、オペレーターに対する高度な訓練が必要です。さらに、財務的な投資も重要な考慮事項となります。このため、一部の製造業者は他社に比べて多層基板製造市場への参入が遅れているのが現状です。
ベンチュアン電子は、以下のような厳しい要件を持つ高度なプリント基板設計をサポートするための拡張機能を提供しています:
· レーザー穴あけによるマイクロビア
· キャビティ基板
· 最大30オンスのヘビーカッパー
· ビアインパッド技術
· マイクロ波およびRF基板
· 最大100層の多層基板
多層プリント基板を始める
- ブラインドビア、バリードビア、ウルトラHDIプリント基板
- 高周波低損失基板材料
- 低損失高速基板材料
- R-5775, R-5785, R-5795, TU-872 SLK , TU-872 SLK SP, TU 933+, I-Tera MT40, Astra MT77, Tachyon 100G 材料
- EM-888, EM-888(S), EM-888(K), EM-526, EM-528, EM-528K, IT-968, IT-968 SE, IT-988G, IT-988G SE 材料