- ブラインドビア、バリードビア、ウルトラHDIプリント基板
- 高周波低損失基板材料
- 低損失高速基板材料
- R-5775, R-5785, R-5795, TU-872 SLK , TU-872 SLK SP, TU 933+, I-Tera MT40, Astra MT77, Tachyon 100G 材料
- EM-888, EM-888(S), EM-888(K), EM-526, EM-528, EM-528K, IT-968, IT-968 SE, IT-988G, IT-988G SE 材料
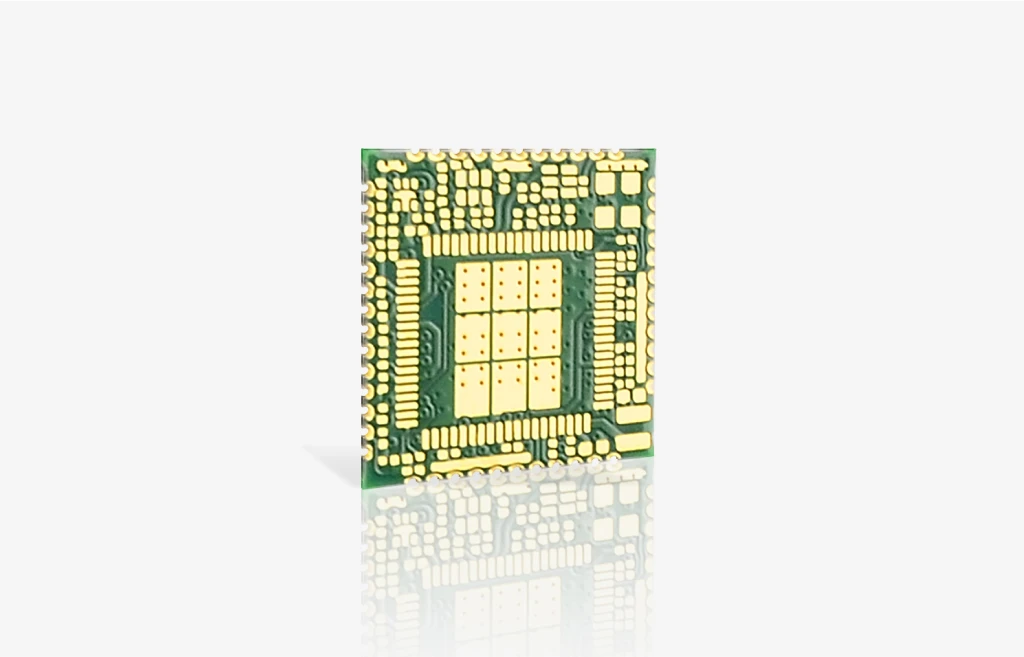
マイクロビアPCB
マイクロビアは、PCB(プリント基板)の1層または複数の層を貫通する微細な穴で、直径は通常0.1mmから0.15mmの範囲です。この小さな構造は、基板の異なる層間で信号や電力を接続するための経路として機能し、高密度インターコネクトを可能にします。
これらの小型構造は、PCBの内層にトレースを到達させ、高い接続密度と高層数の設計を実現します。マイクロビアは以前から存在していましたが、単一の回路基板上で複数の機能が求められるシステムにおいて、その採用がますます一般的になっています。基板設計において、6ミル(約0.15mm)以下のトレース幅が必要であると判断された場合、その設計は高密度であり、層間の配線をサポートするためにマイクロビアが必要になる可能性が高いです。
マイクロビアは、通常のビアを非常に小型化したものですが、その構造には少し違いがあります。マイクロビアは円錐台の形状をしており、層間の移行に伴い内側に傾斜し、次の層のパッドで終端します。最大の信頼性を確保するため、理想的にはマイクロビアは1層のみを貫通する設計が推奨されます。しかし、設計者はスタックドマイクロビアを使用して複数の層にわたる接続を形成することも可能です。この場合、ブラインドビアや埋め込みビアが積み重ねられ、複数層をまたぐ接続が実現されます。
マイクロビアPCBのビア構造
高密度インターコネクト(HDI)は、IPC-2226によって6つの設計タイプに分類されています。これらは、スタックアップ特性に基づいて以下のカテゴリに分けられます:タイプI、タイプII、タイプIII、タイプIV、タイプV、タイプVI。
タイプI
1 [C] 0 または 1 [C] 1
タイプII
1 [C] 0 または 1 [C] 1
コア内に埋め込みビアを持ち、表面から表面まで接続するスルービアを含む場合がある構造。
タイプIII
2 [C] 0
コアまたは表面から表面までのスルービアに2層以上のHDI層を追加した構造。
タイプIV
1 [P] 0
Pは電気的接続機能を持たないパッシブ基板を指す構造。
タイプV
コアレス構造
層ペアを使用した構造。
タイプVI
コアレス構造の別設計
層ペアを使用した代替的な構造
ブラインドマイクロビア
ブラインドマイクロビアは、表面層から始まり、1層下で終端します。ただし、アスペクト比を低く抑えることができれば、2層下で終端することも可能です。2層をまたぐ必要がある場合は、スタックドマイクロビア(後述)またはスタッガードマイクロビアを使用する方が信頼性が高くなります。ブラインドマイクロビアは、充填される場合と未充填の場合があります。
埋め込みマイクロビア
埋め込みマイクロビアは、基本的にはブラインドビアと同じ構造を持ちますが、基板の内部層間を接続し、表面には達しません。ブラインドマイクロビアと同様に、アスペクト比を低く保ち、1層のみをまたぐ設計が、信頼性と製造のしやすさを確保するために最適です。これらのビアは、純銅のメッキプロセスまたはエポキシ+銅樹脂を使用して充填され、マイクロビアのヘッド全体で強固な接続を確保します。メッキプロセスが空隙のない構造を形成することが重要であり、これが最大の信頼性を保証します。
スタックドビアおよびスタッガードビア
スタックドマイクロビアは、高密度配線や低ピッチBGAのファンアウトに必要なスペースを増やしますが、PCBのコストを上昇させます。スタックドビアは、デザインにスタッガードビアを使用する余地がない場合にのみ採用することが推奨されます。埋め込みビア上にスタックされたマイクロビアには、埋め込みビアに対して追加の銅キャップメッキプロセスが必要であり、マイクロビア上にスタックされたマイクロビアには、内部層のマイクロビアを追加の銅で充填する必要があります。
低アスペクト比マイクロビアを形成する層ごとのプロセスにより、スタックアプリケーションに適しています。スタックドマイクロビアは、埋め込みビアのスタック、または埋め込みビア上に配置されたブラインドマイクロビアを指します。これは、HDI PCBで複数の層間を接続する標準的な方法です。スタック内の内部埋め込みビアは、導電性ペーストで充填され、メッキされて次のビアが堆積・メッキされる際に強固な接続を確保します。スタックドマイクロビアの代替として、スタッガードマイクロビアがあります。スタッガードマイクロビアでは、連続する層のマイクロビアが互いにオフセットされています。
HDIマイクロビアの製造
ビアのサイズによって、機械式ドリル加工とメッキ(各層を積層しプレスした後に実施)で形成するか、高出力レーザーを用いて形成するかが異なります。後者のプロセスは、常に改良が進んでおり、高スループットを実現するため、大量生産のPCB製造では優先的に使用されています。最新のレーザードリル技術では、マイクロビアのサイズを15µmまで小型化することが可能になっています。
ドリル加工および洗浄後、ビアホールはスパッタリング、電解メッキ、または無電解銅メッキプロセスのいずれかでメッキされます。メッキプロセスの目的は、充填ビア内に空隙、窪み、突起、またはその他の構造的欠陥が発生するのを防ぐことです。空隙は、応力が集中しやすい部分であり、特に銅が薄くなった空隙の縁で信頼性の懸念となります。
製造工程において、レーザードリルで形成されたマイクロビアは、通常のビアに比べて製造欠陥が発生する可能性が低くなります。一方、機械式ドリルによるマイクロビアは、ドリルの摩耗に伴う振動が原因で欠陥が発生する可能性があります。さらに、機械式ドリルによるマイクロビア加工は、製造業者の工具能力にも依存しますが、直径6~8ミル(約150~200µm)までしか対応できません。
充填済みまたは未充填のマイクロビア
マイクロビアは、銅で充填することも、未充填のままにすることも可能です。埋め込みマイクロビアの場合、特にスタックされる場合には、ビアホールを銅で充填することが必要です。ビアバレル内部に空隙が存在すると、リフロー中に早期破損の原因となる可能性があります。一方、ブラインドマイクロビアは未充填でも問題ない場合がありますが、パッド内に配置されるブラインドマイクロビア(インパッドマイクロビア)は常に充填する必要があります。
充填後、製造業者はマイクロビアをメッキします。このプロセスでは、エポキシと銅樹脂、または純銅が通常使用されます。プロセスは、最初にコンフォーマルコーティングを行い、その後、パルスメッキを使用してマイクロビア本体を固体銅で充填します。これにより、空隙を完全に排除します。メッキプロセス中には、充填材に添加剤を使用することが必要です。添加剤がないと、空隙が形成される可能性があります。また、添加剤の使用は、銅がビアの壁面や上部表面に集中しないようにするためでもあります。マイクロビア本体への銅の不均一な堆積は、コンフォーマルメッキの結果として発生することがあり、これが空隙の形成につながる可能性があります。均一な充填と堆積を確保するために、適切なプロセス管理が不可欠です。
ビア充填オプション
復習すると、ビアとは、PCB内で2層以上を接続するために使用される銅メッキされた穴のことです。ビア充填は、エポキシを使用してビアホールを選択的かつ完全に閉じる特殊なPCB製造技術です。PCB設計者がビアを充填したいと考える場面は多くあり、以下のような主な利点があります:
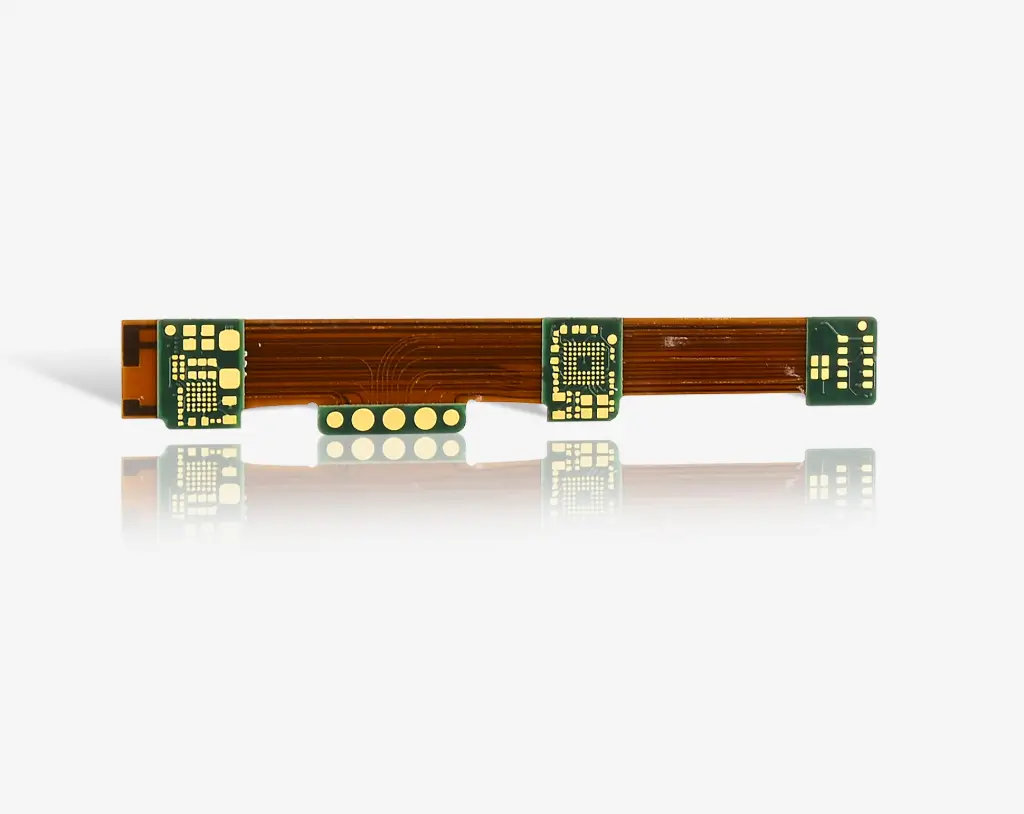
インパッドビア
ビア充填の大きな利点の一つとして挙げられるのが、インパッドビアの実装が可能になることです。このプロセスは、従来の「ドッグボーン」方式(BGAからビアを介して信号を内層に伝送する方法)よりも一般的であり、ますます好まれるようになっています。このプロセスは「アクティブパッド」とも呼ばれ、ビアを充填し、平坦化した後、銅でメッキします。インパッドビアプロセスはコストを増加させる可能性がありますが、従来のスルーホール技術と比較して多くの利点をもたらします。
主な利点:
- BGAピッチの縮小
- 熱放散能力の向上
- 層数や基板サイズの削減(最終的にコスト削減につながる場合もある)
- 配線密度の向上(1層あたりの密度増加)
- パッド接合部の強化
- 高周波設計において、バイパスコンデンサまでの最短経路を提供
- 低インダクタンスなど、高速設計における問題や制約を克服
導電性ビア充填
導電性ビア充填は、回路基板の片側からもう一方への電気信号を効率的に伝送しながら、ビアの熱伝導特性を向上させます。導電性充填ビア(最も一般的なのは銅または銀)は、大量の熱を部品から逃がすのに特に役立ちます。充填材の金属特性により、ICからの熱が効果的に引き出されます。
· 銀エポキシ:コスト効率が高く、より一般的に使用されますが、熱伝導性の点では銅導電エポキシの方が優れています。
· 銅導電エポキシ:熱伝導性に優れています。
両方とも、ビアとPCB内部層間の電流伝導品質を向上させます。ただし、導電性ビア充填は非導電性充填の約5倍のコストがかかる点に留意する必要があります。
非導電性ビア充填
非導電性ビア充填は、導電性充填と同様のプロセスで行われますが、主に熱や信号を伝導する目的ではなく、ビア内へのはんだやその他の汚染物質の侵入を防ぐために使用されます。また、インパッドビアの場合、穴を覆う銅パッドの構造的サポートを提供します。ただし、ビアは依然として銅でメッキされているため、熱と電気信号を伝導します。従来のビアとの唯一の違いは、空洞部分が充填材料で置き換えられている点です。
使用するビア充填材のCTE値を周囲の積層材と一致させることが常に推奨されます。これにより、将来的な収縮や膨張による応力破壊を防ぐことができます。ビア充填材は積層材よりも急速に加熱・膨張するため、この不均一な膨張がパッドと穴壁の間に破損を引き起こす可能性があります。
銅メッキ密閉型充填ビア
多くのPCB設計者はエポキシを使用したビア充填の経験がありますが、スルーホールビアやマイクロビアに対して銅メッキ密閉プロセスを使用する方法にはあまり馴染みがないかもしれません。このプロセスを実行するための適切な設備を持つPCB製造業者が限られているためです。
ベンチュアン電子では、直径12ミル(約0.3mm)までのスルーホールビアを、空隙、気泡、液体の閉じ込めを気にせずに密閉メッキするプロセスを開発しました。このメッキ密閉ビアは、他のビア充填ソリューションの10倍の熱伝導率を提供するため、熱拡散の最適な選択肢となります。
一般的に、アスペクト比が10:1に達する場合やビア径が8ミル(約0.2mm)以下の場合、銅メッキ密閉が適用されます。ただし、他にもビアの充填や密閉が困難な特定の条件があります:
- 薄い材料や基板(20ミル以下)
平坦化プロセスを通過する際に、材料が破れたり歪んだりする可能性が高く、処理が困難になります。 - ラップメッキが必要な場合
終端面に銅のビルドアップが発生し、細線や狭間隔の処理が難しくなります。 - PTFE/テフロン材料
この材料は劇的に歪むため、プロセスがさらに困難になります。
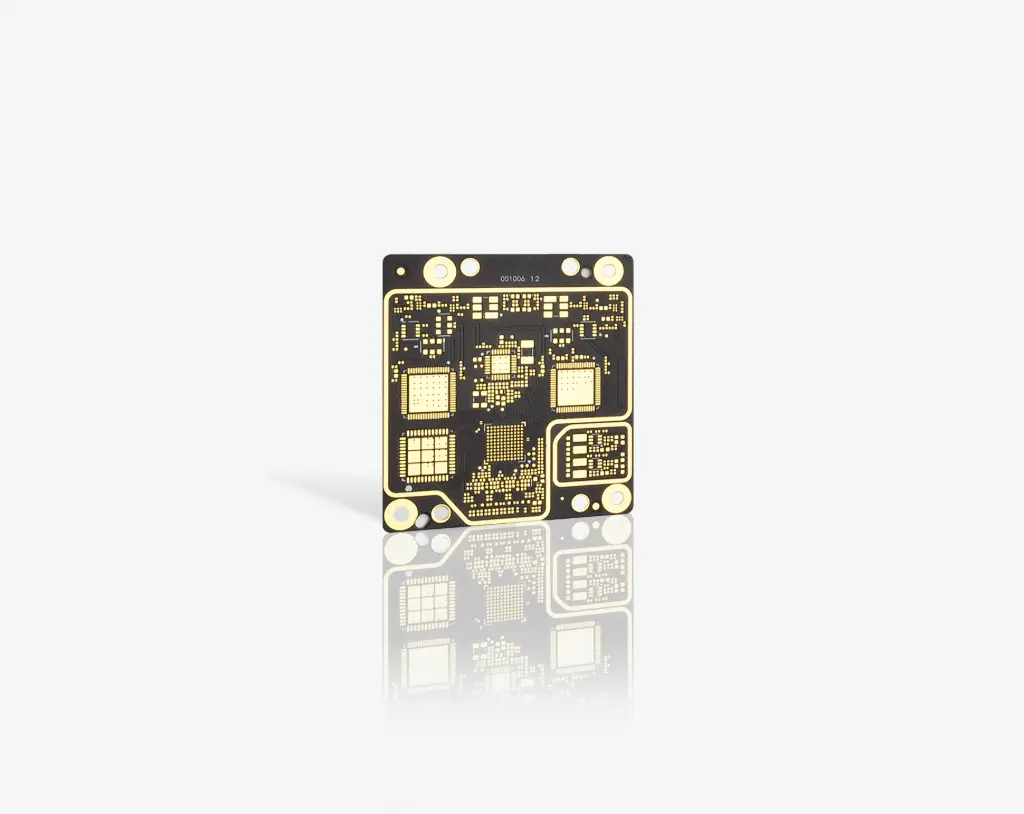
スタッガードマイクロビア
スタックドビアと同様に、スタッガードビアも基板の異なる層を接続します。しかし、それぞれのビアのドリル軸は異なり、隣接層間で位置がずれているため、直接接触することはありません。
スタッガードマイクロビアの設計は、スタックドビアに比べて工程が少なくて済みます。レーザードリルで形成された穴が下層の穴の真上に位置しないため、銅での充填が不要であり、設計が比較的シンプルになります。
スタッガードビア構造を設計する際、主な懸念事項はレーザードリルされた穴同士の間隔です。スタッガードビア設計の実現可能性は、隣接するマイクロビアの中心間の垂直距離に依存します。適切なスタッガード設計では、この垂直距離がマイクロビアの直径を超える必要があります。
スタックドマイクロビアは、ビア壁に圧力をかけることがあります。この圧力により、最上部のビアがパッドから剥離する可能性があります。そのため、2層以上を接続する必要がある場合、設計者はスタッガードマイクロビア構成を好む傾向にあります。
しかし、設計にスペースの制約がある場合、スタッガードビアは適切でない場合があります。スタッガード構造は複雑さが少ないものの、基板上でより多くのスペースを消費します。一方で、スタッガード構造はビアの位置がオフセットされているため、クロストークの問題はほとんど発生しません。ただし、スタッガード構造では信号経路により多くの不連続性が生じます。このため、高速設計において均一なビアインピーダンス要件を維持することが難しくなる可能性があります。
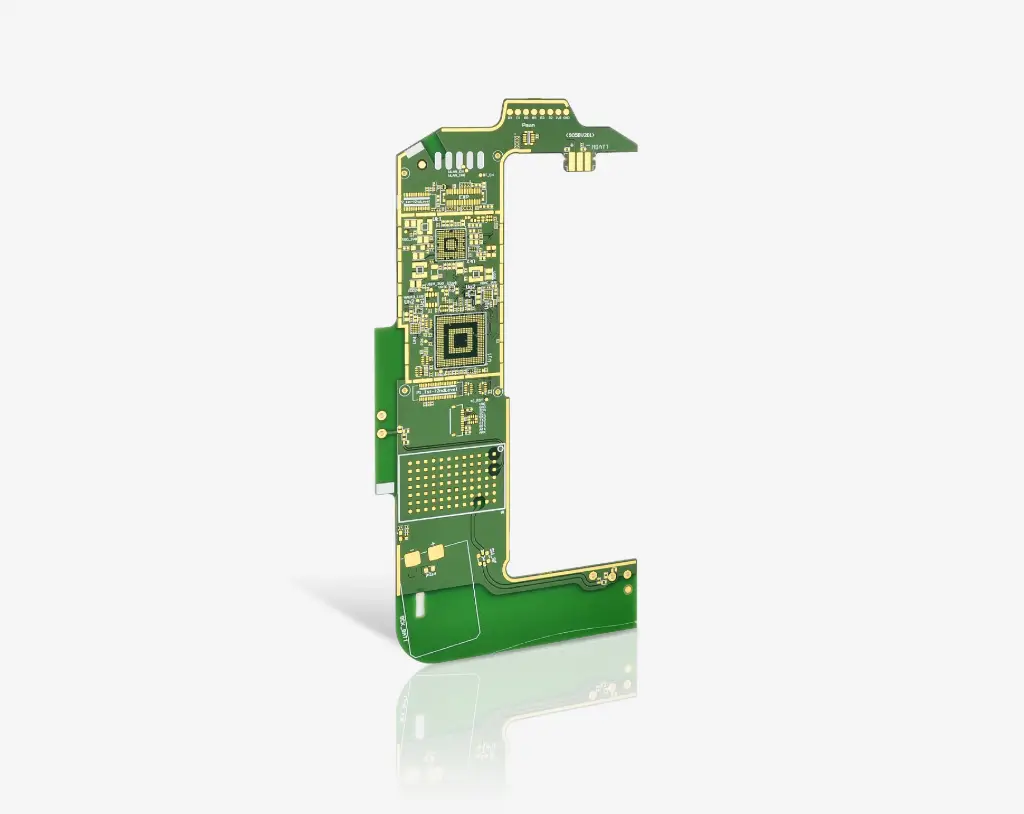
スタックドマイクロビア
スタックドビアは、ビアが垂直に積み重ねられる構造です。オペレーターは、各ビアをドリルで加工し、メッキ処理を行った後、他のビアの上に積み重ねて複数の層を接続します。この構造では、上部と下部にそれぞれ狭いアニュラリングが使用されます。上部のアニュラリングは正確な位置合わせを助け、下部のリングは電気的接続を行います。
スタックドビアは、電解銅メッキで充填されます。これにより構造的なサポートが提供されると同時に、確実な電気接続が保証されます。ただし、不適切なメッキ処理が行われると、ビア底部と下層のターゲットパッドとの間に空隙や接着不良が発生し、スタックドビアの信頼性を損なう可能性があります。
スタックドビアの主な利点は、そのコンパクトさにあります。HDI基板では、スタックドビアが実用的な配線の柔軟性を提供します。さらに、信号の送信元から送信先までの適切に制御されたインピーダンスを維持するのにも役立ちます。
誘電体のZ軸方向からの圧力がマイクロビアの信頼性に影響を与える場合があります。これは、使用材料の熱膨張係数(CTE)の不一致が原因です。例えば、ガラス転移温度を超えた場合、銅の膨張は1,000,000分の16(16ppm)に留まるのに対し、誘電体は1,000,000分の200(200ppm)まで膨張します。
単層の場合、この不一致は大きな問題を引き起こしません。しかし、層数が2層以上になると、問題が顕在化します。例えば、層数が3層以上の場合、不一致が許容範囲を超え、ビアバレルやコーナーの亀裂によるマイクロビアの故障につながる可能性があります。この問題を回避するため、設計者はビアを垂直にスタックするのではなく、スタッガード(ずらす)配置を採用することが一般的になりました。
マイクロビアプリント基板を始める
- ブラインドビア、バリードビア、ウルトラHDIプリント基板
- 高周波低損失基板材料
- 低損失高速基板材料
- R-5775, R-5785, R-5795, TU-872 SLK , TU-872 SLK SP, TU 933+, I-Tera MT40, Astra MT77, Tachyon 100G 材料
- EM-888, EM-888(S), EM-888(K), EM-526, EM-528, EM-528K, IT-968, IT-968 SE, IT-988G, IT-988G SE 材料