- 高周波低損失基板材料
- 低損失高速基板材料
- R-5775, R-5785, R-5795, TU-872 SLK , TU-872 SLK SP, TU 933+, I-Tera MT40, Astra MT77, Tachyon 100G 材料
- EM-888, EM-888(S), EM-888(K), EM-526, EM-528, EM-528K, IT-968, IT-968 SE, IT-988G, IT-988G SE 材料
- 高密度相互接続(HDI)プリント基板は、マイクロビア(Microvia)、パッド内ビア(Via-in-Pad)、および微細な配線/間隔(Trace/Space)を採用することで、より高い信号密度と優れた信号品質(Signal Integrity)を実現します。
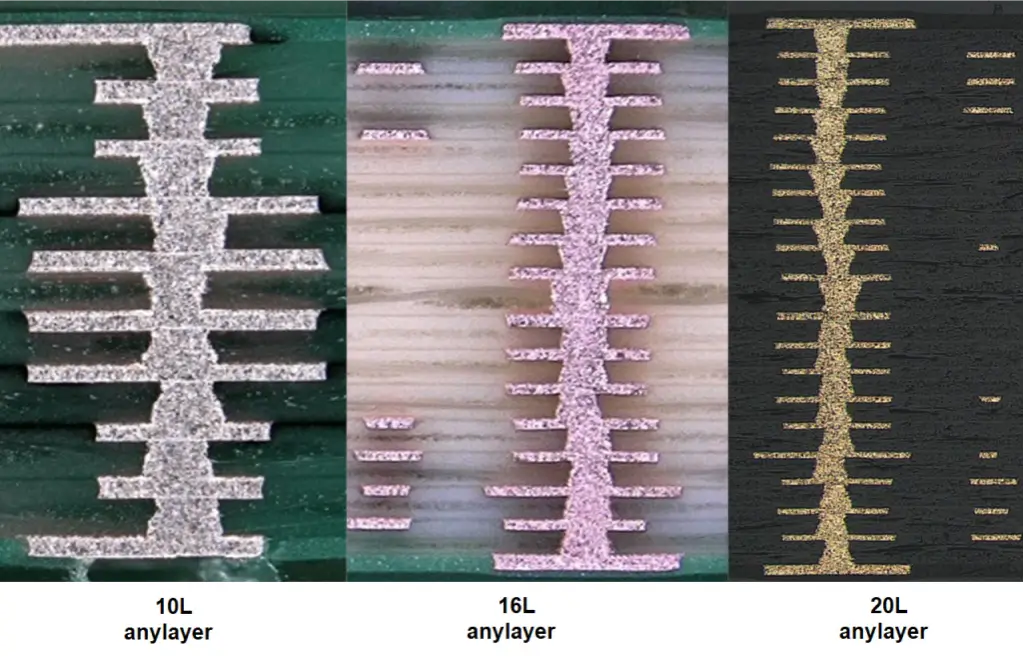
ビルドアップ基板
IPC-2226では、HDI(高密度インターコネクト)基板を、従来のプリント基板(PCB)よりも単位面積あたりの配線密度が高い基板として定義しています。また、IPC-2226ではHDI基板の特長をタイプI、タイプII、タイプIIIの3種類に分類しています。
高密度インターコネクト(HDI)プリント基板(PCB)は、標準的なPCBに比べてはるかに高い回路密度を有しており、より小さな面積に多くの部品を配置することが可能です。これを実現するために、以下の技術が活用されています:
· トレース幅の縮小
· 層数の増加
· スタックビア、スタッガードビア、ブラインドビア、埋め込みビアの採用
· 微細なラインおよびスペースの活用
HDI基板は、製造プロセスがより複雑で、特殊な材料を使用するため、通常のPCBよりもコストが高くなる傾向があります。以下は、PCB設計者が理解すべき重要な設計上の考慮事項の一部です。設計者は、高度な技術を用いる基板における課題を製造業者が十分に理解していることを確認する必要があります
ベンチュアン電子は、高密度インターコネクト(HDI)基板の製造および加工を含むあらゆる案件に対応できる能力と経験を有しています。HDI基板は近年ますます普及しており、医療、軍事、航空宇宙産業をはじめとする幅広い分野で使用されています。特に、スマートフォン、タブレット、その他のデジタルデバイスにおいて顕著に採用されています。
HDI多層基板の対応能力
HDI基板は、特に細ピッチBGAコンポーネントや高密度配線が必要な場合、層間を接続するために小型ビアが求められます。細ピッチ部品に対応するため、HDI設計には以下のような典型的な特徴が含まれます:
小型ビア:HDI基板では、マイクロビア(機械式またはレーザー加工)、ブラインドビア、埋め込みビア、スタッガードビアが層間接続に使用されます。これらのビアは、通常のスルーホールビアよりもアスペクト比が小さく、直径も小さいため、使用可能な深さに制限があります。
細い配線:HDI基板では、各層のビアやインパッドビアに接続するために細い配線が必要です。細い配線は、配線密度を高めることも可能にし、これが「高密度インターコネクト(HDI)」という名称の由来となっています。
高い層数:HDI基板では高ピン密度の部品(例:FPGA)を扱う際、層数が20層以上に達することが一般的です。非HDI基板でも高層数の構造は可能ですが、HDI基板では特に層数の多い設計が求められます。
低い信号レベル:HDI基板は高電圧や大電流を扱う用途には適していません。これは、隣接する配線間の高い電界強度が静電放電(ESD)を引き起こし、高電流が導体の過剰な温度上昇を引き起こすためです。
HDI PCB設計ガイドライン
HDI基板設計ガイドラインをダウンロード
初期段階からの設計ミスを防ぐために、チェックリストとして活用できる設計ガイドラインをまとめました。
このファイルには、HDI基板に一般的に関連する製造特性が記載されています。ただし、記載されている仕様の限界値は網羅的ではありません。当社の経験豊富なエンジニアは、あらゆる種類のPCB材料を取り扱ってきた実績があり、その知識と専門性を活かして推奨事項を提供し、HDI基板に関するすべての質問にお答えします。さらに重要なこととして、製造可能性に関する支援や、プロジェクトの潜在的なコスト要因に関するアドバイスを的確に行うことができます。
Description | Production | Advanced |
---|---|---|
Structure | 3+n+3 (8+N+8 MAX) | 9+N+9 |
Layer Count | 2~80L | 100L |
Min. Board thickness | 0.005" (+/-10%) | 0.005" (+/-10%) |
Max. Board thickness | 0.300" (+/-10%) | 0.350" (+/-8%) |
BGA Pitch | 8mils (0.2mm) | 6mils (0.15mm) |
Min.BGA pad/space | 7mils/3mils | 5mils/2mils |
Materials for build up | ||
Prepreg (FR4 1067/1086/2113) | Yes | Yes |
Prepreg (ceramics Ro4350) | Yes | Yes |
Laser Drillable Prepreg | Yes | Yes |
laser Drillable core (FR4, PI, PTFE, ceramics) | Yes | Yes |
laser Drillable Min.Dielectric thickness | 2mils | 1.5mils |
laser Drillable Max.Dielectric thickness | 4mils | 5mils |
Laser via | ||
Min / Max | 2.5mils / 6mils | 2mils / 6mils |
Min via edge to via dege space | 6mils | 5mils |
True position Tolerance | +/-1mils | +/-1mils |
Drilling | ||
Min. Drilled blind via diameter (as drilled) | 6mils | 5mils |
Min via edge to via dege space (as drilled) | 8mils | 7mils |
PTH Design | ||
Blind via aspect ratio (dielectric thickness/ Laser drill hole size) | 0.8 | 1 |
Blind via plating thickness | 0.3~1mils | 0.3~1mils |
Capture pad A/R | 2.5mils | 2mils |
Laser via Fill Material | Epoxy resin/Copper paste | Epoxy resin/Copper paste |
Blind via aspect ratio (as drilled) (dielectric thickness/ drilling hole size) | 0.5 | 0.5 |
Blind via plating thickness (as drilled) | 0.8mils | 1.0mils |
Capture pad A/R (as drilled) | 3mils | 2mils |
Outer Layer | ||
Min. Trace/Space | 2mils / 2mils | 1.5mils / 1.5mils |
Min. pad over drill size | 6mils | 5mils |
Max. Copper thickness | 12 oz | 30 oz |
Line/ pad to board edge | 8mils | 7mils |
Line Tolerance | +/-15% | +/-10% |
Inner Layer | ||
Min.Trace/Space | 1.5mils / 1.5mils | 1.2mils / 1.5mils |
Min. Copper Thickness | 1/3oz | 1/7 oz |
Max. Copper Thickness | 10oz | 12oz |
Min. Core Thickness | 2mils | 1.5mils |
Line/ pad to drill hole | 7mils | 6mils |
Line/ pad to board edge | 8mils | 7mils |
Line Tolerance | +/-10% | +/-10% |
もっと見る +
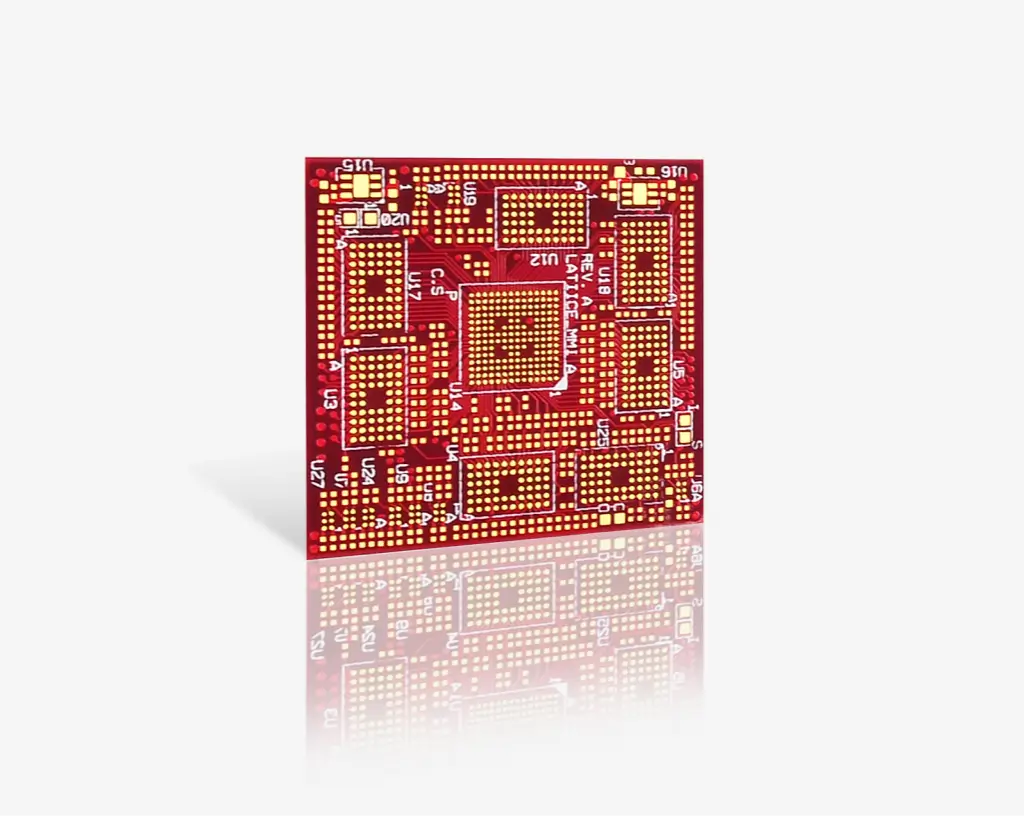
HDI PCB 1-N-1
これは最もシンプルなHDI基板設計構造で、I/O数が少ないBGAに適しています。この構造は、0.4mmのボールピッチに対応可能な細線、マイクロビア、および高精度な位置合わせ技術を備え、優れた実装安定性と信頼性を提供します。また、銅充填ビアを含む場合があります。
1-N-1スタックアップでは、「1」はコアの両側に1回の順次積層を表します。1回の順次積層により、2つの銅層が追加され、合計でN+2層となります。この構造ではスタックビアは使用されません。追加の積層は1回のみで、ビアのスタッキングはありません。埋め込みビアは機械的にドリル加工されており、導電性充填材は不要で、誘電体材料で自然に埋まります。2回目の積層で上下の層が追加され、最終的に機械的ドリル加工で仕上げます。製造業者は、1層目と2層目の間に適切なプリプレグを配置し、樹脂が埋め込みビアに流れ込むよう計画します。
HDI PCB 2-N-2
PCB製造における2+N+2は、プリント基板の設計におけるスタックアップ構造を指します。「2」と「2」は、基板のコアにある銅層(または他の材料)の数を表し、これが部品の電気的接続と安定性を提供します。「N」は、コア層間に追加できる信号層の数を指します。「N」の値は、PCBの複雑さや電気接続の必要性によって決まります。
例えば、プリント基板の順次積層における「4+N+4」は、PCBの製造プロセスで使用される層数を示します。
このスタックアップ構造は、PCBの全体的な電気性能、信号の整合性、熱管理を決定する上で重要です。コアに4層、内部に追加のN層を設けることで、設計者はルーティング、シールド、デカップリング戦略を最適化し、基板の電気的要件を満たすことができます。さらに、コアにある追加の4層が基板の機械的強度を向上させます。
全体として、4+N+4のスタックアップ構造は、必要な電気性能、信頼性、機械的強度を提供するバランスの取れた設計です。
Any Layer PCB
「Any Layer PCB(任意層HDI基板)」は、レーザー技術と充填メッキ技術を組み合わせることで、超微細加工を可能にし、全層間で自由に接続を行うことができる基板です。この高い設計自由度と高密度配線により、スマートフォンやその他の高性能デバイスの小型化や薄型化のニーズに最適です。
「Any Layer HDI PCB」とは、スタックアップ内の任意の層間で高密度インターコネクトを用いて信号をルーティングできる基板を指します。この高度なHDI基板には、銅充填スタックインパッドマイクロビアが複数層含まれており、より複雑な相互接続を可能にします。Any Layer HDI基板では、各層に独自の銅充填レーザードリルマイクロビアが使用されます。この構造により、層間の接続が可能となり、層が積層された後、任意の2層間での接続が可能になります。この設計は高い柔軟性を提供するだけでなく、任意層での接続密度を最大化することも可能にします。
HDIプリント基板の構造
プリント回路基板協会(IPC-2226)は、HDIプリント基板の設計構造を6つに分類しています。これらの設計構造はIPC-2226規格によって定義されており、それぞれ「i+[C]+i」という表記で表されます。「i」は「コア」[C] の両側に配置される層数を示します。PCBのコアは、銅配線がプリントされた硬質基材を指します。以下は、HDIプリント基板の製造で最も一般的に使用される3つの構造です。
IPC-2226規格におけるHDI特徴の分類
- タイプI:マイクロビアを特徴とし、サイズは0.15 mm(6 mil)以下。
- タイプII:ブラインドビアを特徴とし、ビアが基板全体を貫通せず、内部層で終端します。サイズは通常0.15 mmから0.50 mm(6 milから20 mil)の範囲。
- タイプIII:スルーホールビアを特徴とし、ビアが基板全体を貫通し、両面に伸びます。サイズは通常0.50 mm(20 mil)以上。
各タイプのHDI特徴は特定の要件を満たすよう設計されており、それぞれ異なる用途に使用されます。IPC-2226規格は、HDI特徴の設計ガイドラインと性能基準を提供しており、高密度プリント基板の設計および製造における業界標準として広く利用されています。
HDIプリント基板のスタックアップ IPC-2315規格に基づき、製造業者はタイプI、II、III、IV、V、VIのいずれかのHDIスタックアップを使用できます。ただし、タイプIV、V、VIは製造コストが高く、配線やBGAのブレークアウトが困難な高密度PCBには通常適していません。
HDI設計の製造性 HDI設計の製造性は主にビア構造に依存します。マイクロビア構造は製造プロセスに大きな影響を与えます。特に、層間でマイクロビアが開始および終了する箇所が多い場合、PCB製造に必要な積層サイクル数が増加します。層のバリエーションが多いほど、順次積層の回数が増えるため、製造プロセスがより複雑になります。
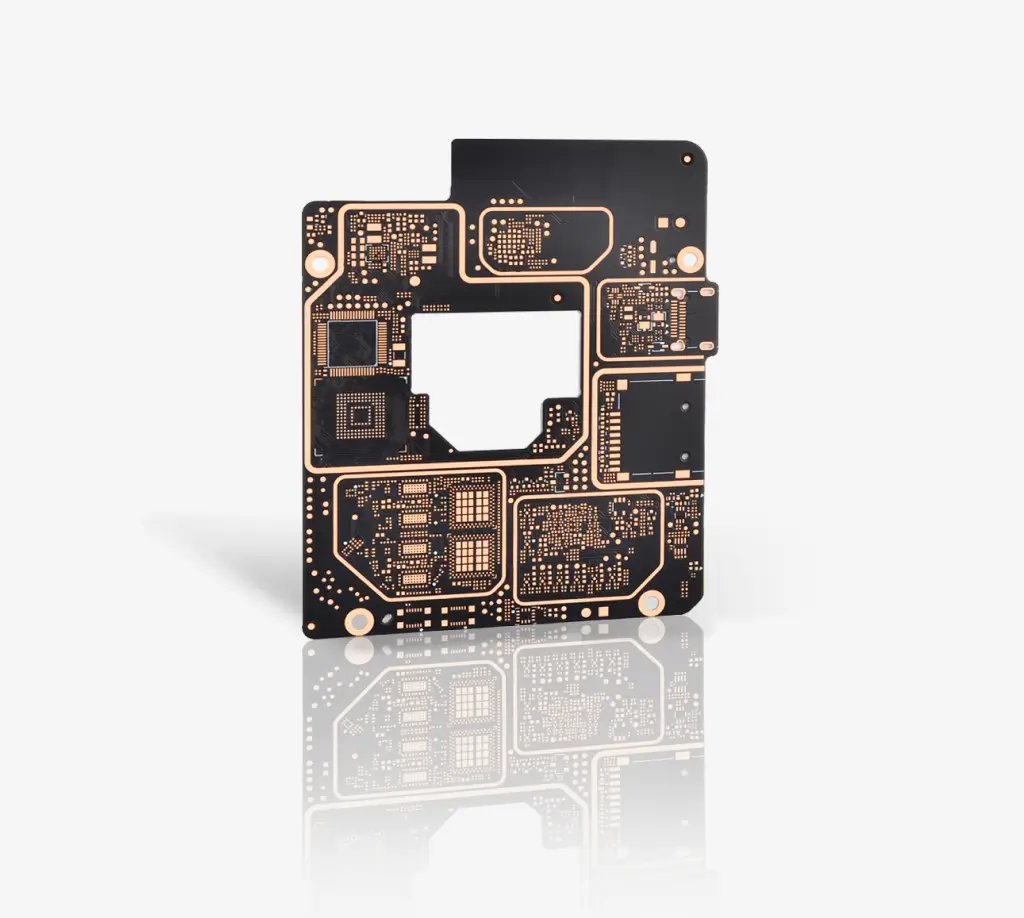
Any Layer HDI PCBの製造
Any Layer HDI PCBの製造プロセスは、レーザードリルで加工されたマイクロビアと、銅で充填された堅固な基材を持つ超薄型コアから始まります。内層に形成された初期のマイクロビアに銅を充填した後、次の誘電体層が順次積層されます。この新しい層に対してレーザードリル加工を施し、Any Layer HDI PCBのスタック構造を構築します。その後、その層のビアに銅を充填します。このプロセスを繰り返すことで、銅充填マイクロビアを使用した所定のスタック構造が完成します。
順次銅充填を行うことで基板の構造的な一体性が向上します。また、スタックマイクロビアを使用する場合、内部のマイクロビアにおける窪みや空隙を防ぐためには、この構造が必要です。ビルドアップ層間で強固なメッキインターフェースが形成されることで、基板の信頼性と耐久性が高まります。
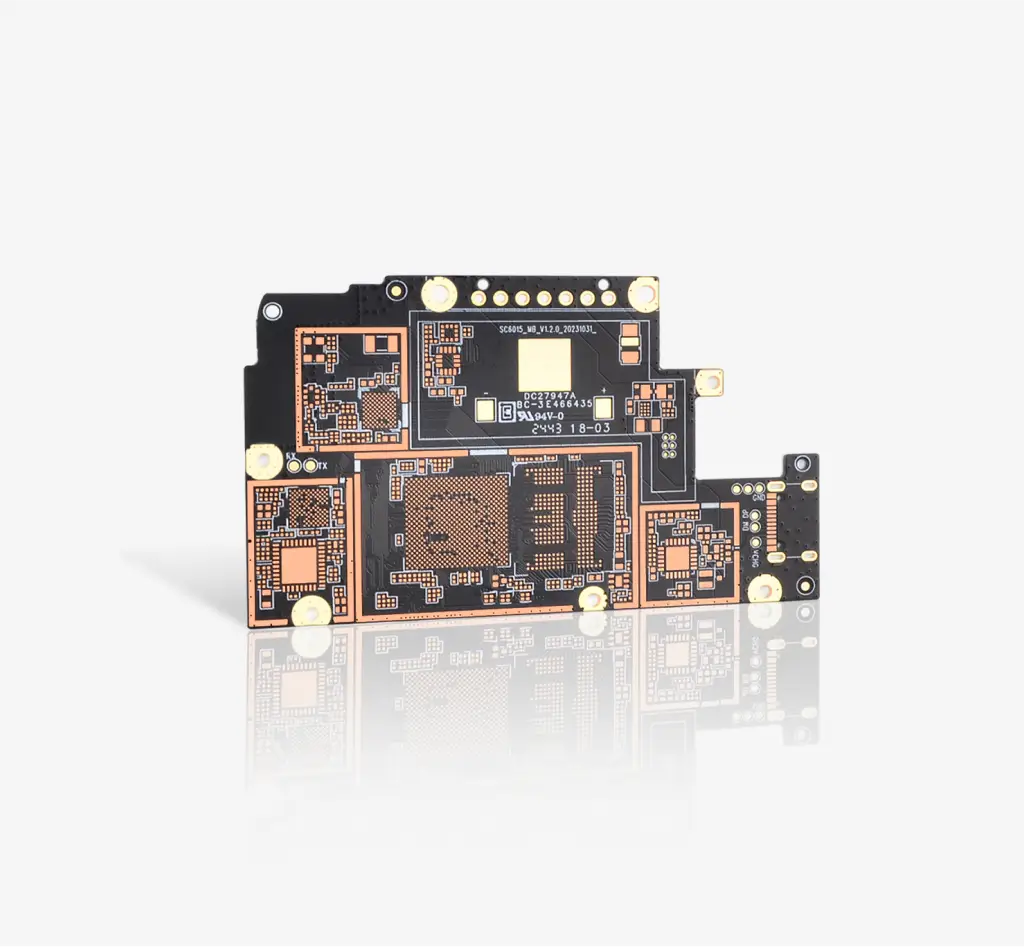
順次積層プロセス
順次積層は、複数の金属層と絶縁材料を順次積み重ねて積層するプロセスであり、複雑で高密度な回路設計を持つ多層PCBの製造に使用されます。このプロセスでは、各層が一層ずつ追加され、各層の上にドライフィルムフォトレジスト材料が塗布されます。その後、エッチングを行い、所定のパターンを形成します。この作業を各層ごとに繰り返し、すべての層が組み立てられた後、全体を加熱と加圧下でプレスし、固体で高密度なPCBを形成します。
各積層サイクル、または順次積層プロセスでは、必要な層数の材料を積み重ねた後、熱と圧力を加えて各層を接着します。このプロセスは、最終的な厚さが達成されるまで各サイクルで繰り返されます。
プリント基板における順次積層サイクルで直面する課題:
- 積層の一貫性:複数の積層サイクルを通じて一貫した積層品質を確保することは大きな課題です。圧力、温度、時間の均一性をコントロールすることが難しく、不均一な積層が生じる可能性があります。
- 剥離:剥離は、プリント基板の層間接着が弱くなるか、失敗することで発生する一般的な問題です。複数回の積層サイクルを経ることで剥離のリスクが高まり、基板の不良を引き起こす可能性があります。
- 反り:反りは、複数回の積層サイクルに関連するもう一つの一般的な問題です。基板が均等に加熱および冷却されないことにより、基板が歪み、反りが生じることがあります。
- 積層欠陥:積層中に気泡、亀裂、空隙などの積層欠陥が発生することがあります。これらの欠陥は基板の強度を低下させ、信頼性を減少させる原因となります。
- 材料の圧縮:複数回の積層サイクルにより、基板の材料が圧縮されることがあります。これにより、基板の元の厚さが失われ、性能や信頼性に影響を与える可能性があります。
HDI基板の適用分野
モバイル:
スマートフォン/タブレット
モバイルデバイスの高機能化のトレンドに対応するため、当社では、小型・高密度・高品質な基板製造プロセスにおいて、ビルドアップスタックビア、スタッガードビア、充填ビア、およびファインピッチ技術を適用しています。
メモリモジュール(DIMM/SODIMM):デスクトップPC/ノートPC/ワークステーション/サーバー
大量データを迅速に処理する性能が求められるPCのパフォーマンス向上のため、当社はさまざまな形式のDIMMおよびSODIMM用のPCBを提供しています。また、サーバーやワークステーション向けにカスタマイズオプションもご用意しています。
SSD:
デスクトップPC/ノートPC/ワークステーション/サーバー
低消費電力かつ高い処理速度を備えたSSD(ソリッドステートドライブ)は、次世代の環境に優しいストレージデバイスとして注目されています。将来的には、PCの標準的なサブストレージデバイスとなるでしょう。現在、当社は多層構造で高品質なPCBを提供しています。
ディスプレイ(LCD/OLED):
OLED TV/PCモニター/ノートPCモニター/モバイル・タブレットディスプレイ
ディスプレイ産業は、情報通信産業の急速な発展に伴い、今後も成長が期待されています。近年では、高解像度、高集積化、薄型化、軽量化が求められています。これに対応するため、当社ではビルドアップスタックビア、スタッガードビア、充填ビア、ファインピッチ技術を採用し、顧客のニーズに応じた高密度・高品質なPCBをさまざまなディスプレイ製品に提供しています。
HDIプリント基板を始める
- ブラインドビア、バリードビア、ウルトラHDIプリント基板
- 高周波低損失基板材料
- 低損失高速基板材料
- R-5775, R-5785, R-5795, TU-872 SLK , TU-872 SLK SP, TU 933+, I-Tera MT40, Astra MT77, Tachyon 100G 材料
- EM-888, EM-888(S), EM-888(K), EM-526, EM-528, EM-528K, IT-968, IT-968 SE, IT-988G, IT-988G SE 材料