- SMT實裝、BGA實裝、通孔實裝、混合實裝
- PCB實裝或整機組裝服務可提供完成的PCBA或完整的電子組裝產品
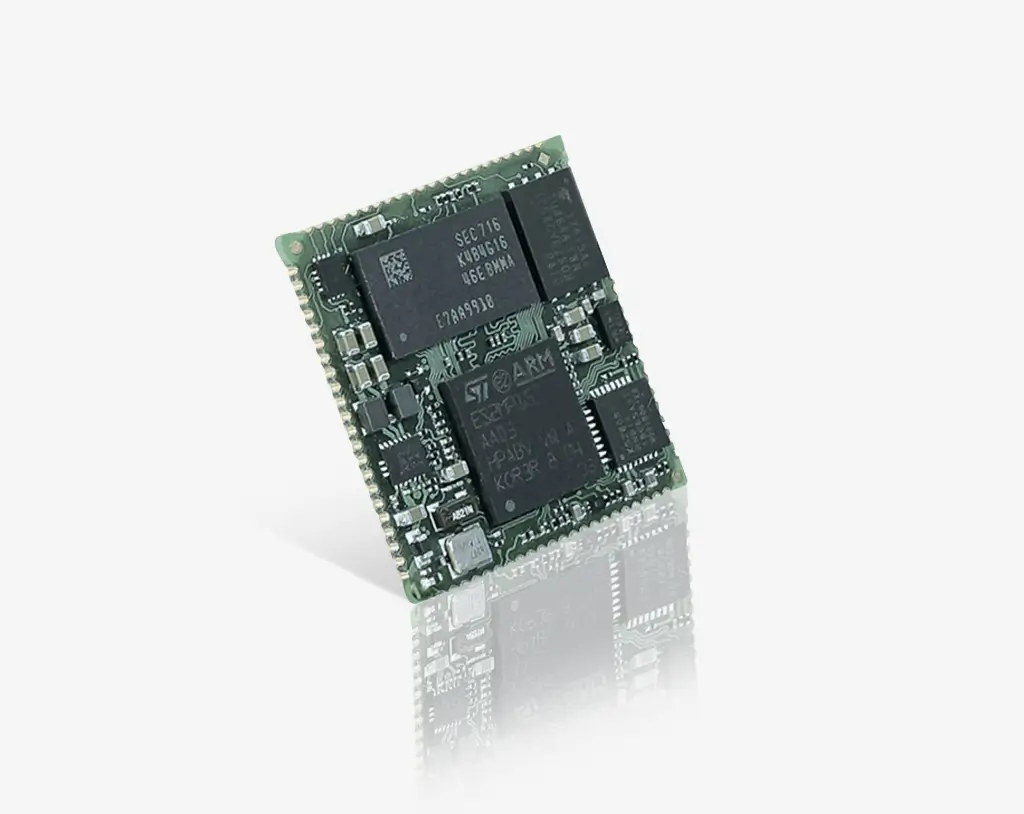
電路板組裝
印刷電路板(PCB)組裝是將電子元件焊接到裸板上的過程。安裝在裸板上的電子元件可以是穿孔元件和/或表面貼裝元件(SMT)。如果組裝中包含兩者,則有時稱為高混合印刷電路板。PCB組裝是電子製造過程的一個環節。其他環節包括電纜/線束、機械/外殼組裝、編程和功能測試。
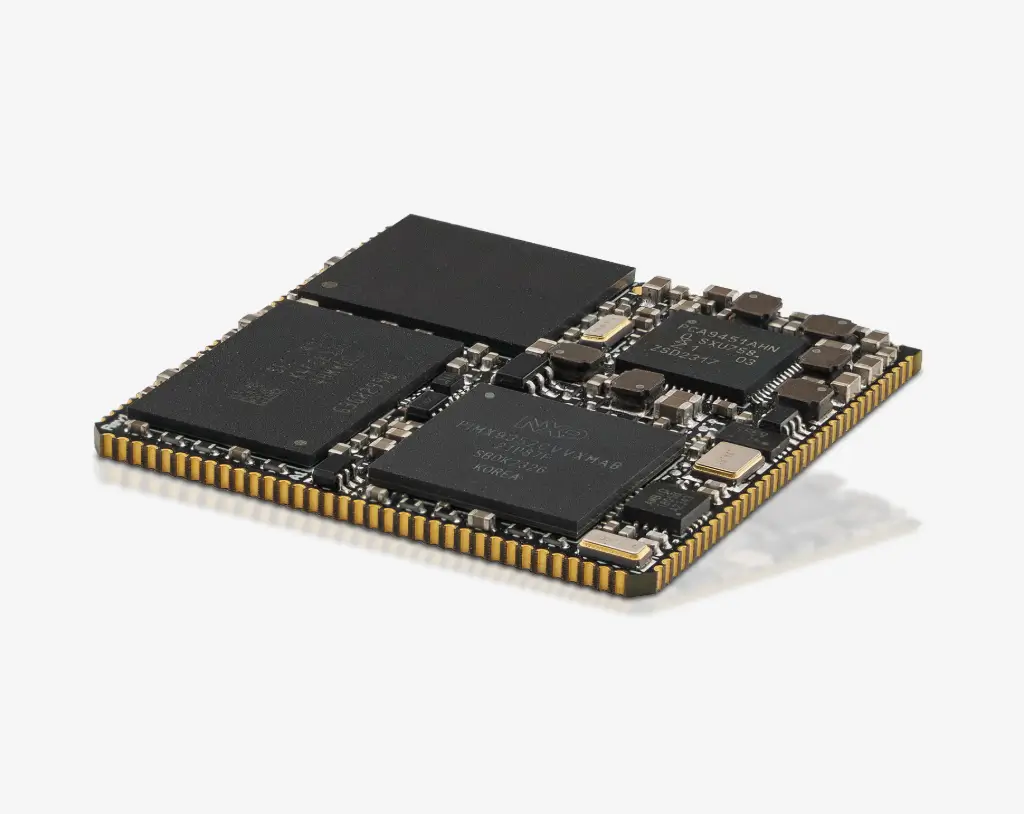
印刷電路組裝包括:
- SMT(表面貼裝技術)、通孔及混合組裝
- 支援最小至01005尺寸的元件
- 球柵陣列(BGA)
- 超細球柵陣列(uBGA)
- 無引腳四方扁平封裝(QFN)
- 四方扁平封裝(QFP)
- 塑料引腳芯片載體(PLCC)
- 小型封裝積體電路,封裝疊封技術(封裝層上封裝)
- 小型芯片封裝(間距0.2mm)
- IC編程
- 功能測試
PCB組裝能力
下載PCB組裝能力
為了避免一開始就出錯,我們整理了設計規範,您可以將其作為檢查清單使用。
該文件列出了與PCB組裝通常相關的一些製造特徵。所列的特徵限制並不全面;我們的經驗豐富的工程師也處理過各種類型的PCB材料,因此他們擁有提供建議和解答所有PCB組裝問題的知識和專業能力。最重要的是,他們知道如何協助實現製造可行性並理解項目的潛在成本驅動因素。
Parts Procurement | Full Turnkey, Partial Turnkey and Kitted/Consigned |
---|---|
Assmebly Types | Surface Mount (SMT), Thru-hole, Mixed Technology (SMT/Thru-hole),Single and double sided SMT/PTH , Large parts on both sides, BGA on both sides |
Largest PCB/Panel Size | 24 x 35ʺ |
Smallest PCB/Panel Size | 1.2ʺ wide |
Largest QFP Size/BGA Size | 75 mm x 87 mm |
BGA Pitch Range | From 0.25 mm to 3 mm |
Smallest QFP Pitch Range | From 0.25 mm to 3 mm |
Stencils | Laser cut stainless steel and Nano-coating |
Components | Passive components smallest size 01005,Fine pitch components smallest size 6 Mils pitch, Leadless chip carriers/ BGA, VFBGA, FPGA & DFN, Connectors and terminals |
Component packaging | Reels, Cut tape, Tube and Loose parts |
Inspection | X-ray analysis, AOI and Microscope to 20X |
Solder Type | Leaded and Lead-free/RoHS compliant |
Assembly surface mount connectors | Yes |
Wave Soldering | Yes |
Conformal Coating And Potting | Yes |
PCB Finish | SMOBC/HASL, Electrolytic gold , Electroless gold , Electroless silver, Immersion gold, Immersion tin and OSP |
Panelized PCB | Tab routed ,Breakaway tabs ,V-Scored and Routed+ V scored |
Design File Format | Gerber RS-274X, 274D, Eagle and AutoCAD’s DXF, DWG BOM (Bill of Materials) and Pick and Place file (XYRS) |
Other Services | Parts Management, IC Programming and Functional Testing |
查看更多 +
PCB 組裝類型
- 表面貼裝(SMT)
- 穿孔元件(Thru-hole)
- 混合技術(SMT/穿孔元件)
- 單面或雙面元件安裝
PCB板組裝焊接類型
- 含鉛
- 無鉛/RoHS符合標準
- 無清潔和水性清潔助焊劑
PCB組裝元件類型
- 支援最小至01005尺寸的元件
- 球柵陣列(BGA)
- 四方扁平無引腳封裝(QFN)
- 四方扁平封裝(QFP)
- 小型芯片封裝(間距0.2毫米)
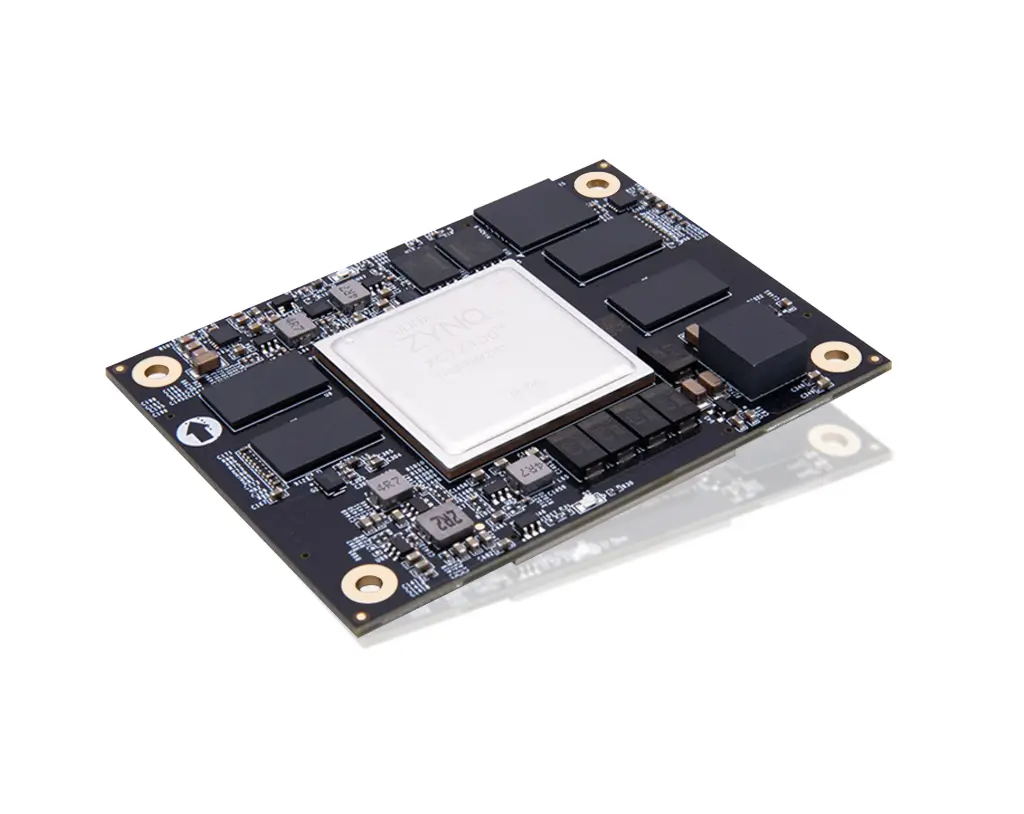
PCB組裝控制與檢查
- 自動光學檢查(AOI)
- 3D自動光學檢查(3D AOI)
- 3D焊膏檢查(3D SPI)
- X射線檢查
- 電路內測試(In-Circuit Testing)
PCB組裝製造設備
我們堅持質量貫穿於所有製程的原則,從頭到尾,質量始終放在首位。我們致力於提供具有成本效益、高品質的PCB組裝服務,並提供卓越的客戶服務。
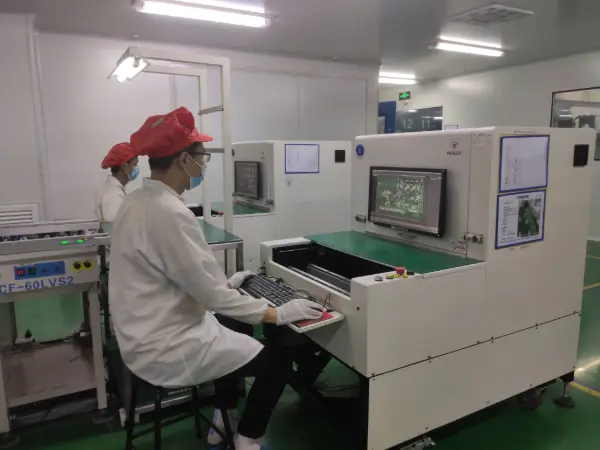
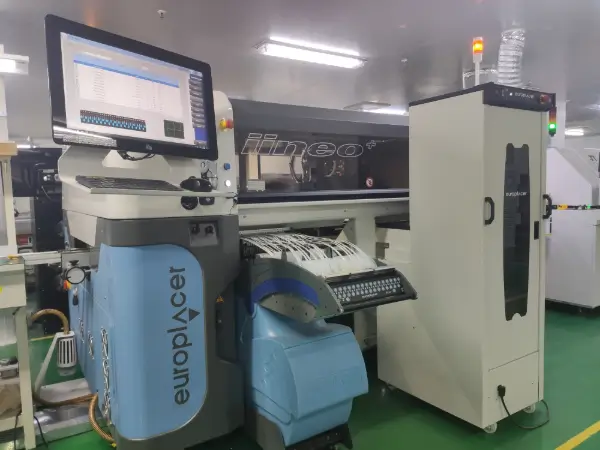
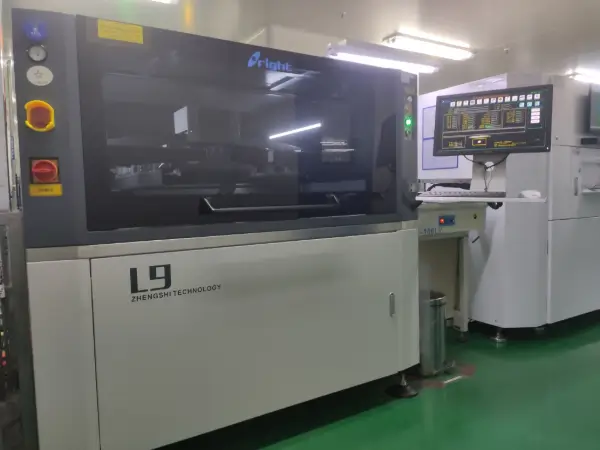
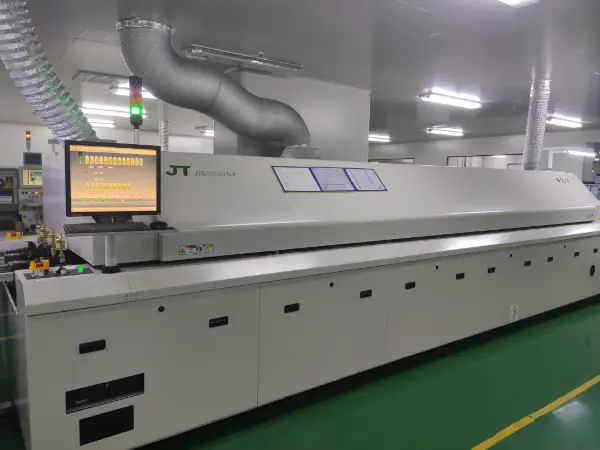
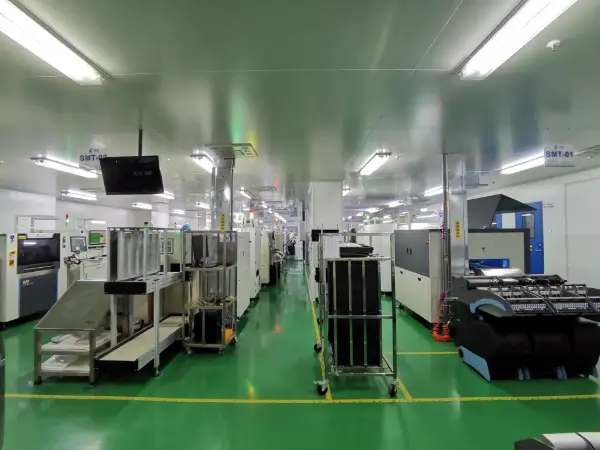
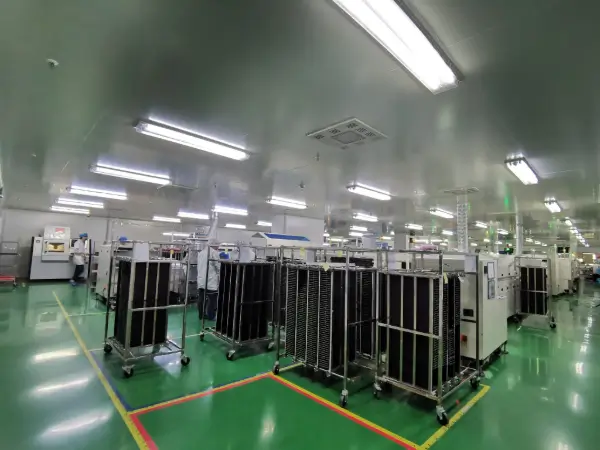
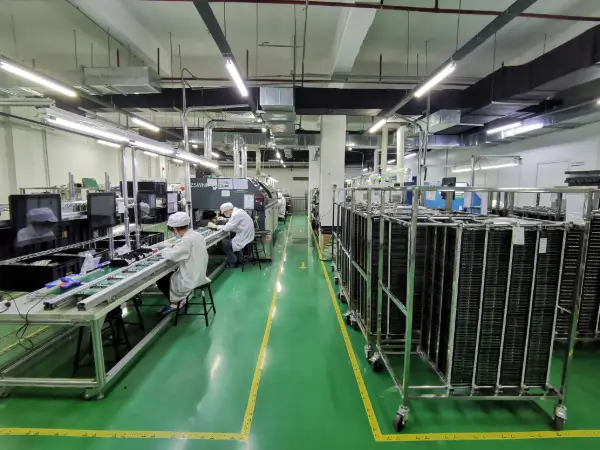
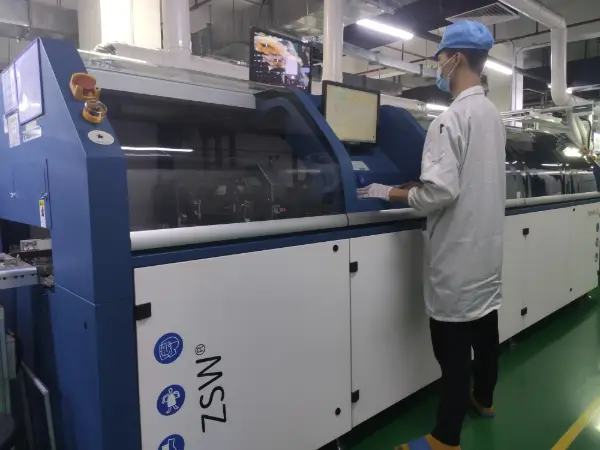
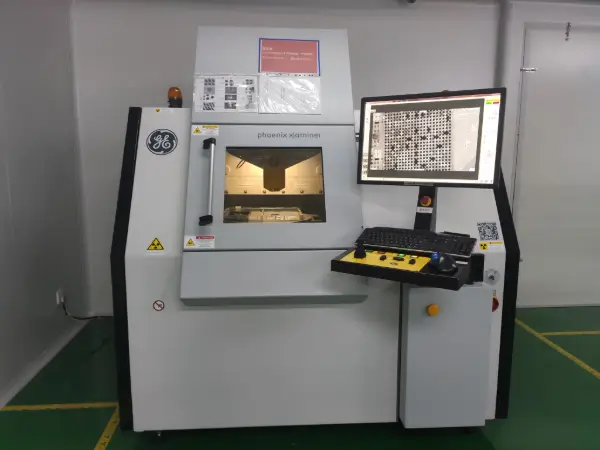
PCB組裝檔案要求
請將以下檔案隨訂單一起提交,並將所有檔案包含在單一的ZIP檔案中。
Gerber檔案
請包含所有層(如銅層、焊膏、絲印、焊接掩膜等)。
元件位置檔案
也稱為點位檔案。應包含元件位置、旋轉角度和參考標識符。
物料清單(BOM)Excel格式。您的BOM應該包含:
- 參考標識符
- 每個元件的數量
- 製造商零件號
- 元件描述
- 類型(SMT、穿孔元件、細間距、BGA等)
- 封裝描述(例如QFN32、SOIC、0805等封裝,封裝描述非常有幫助,但不是必須的)。
印刷電路板組裝檢查清單
奔创电子希望我們的客戶能夠體驗到無縫且精確的組裝過程。為了確保您的訂單不會被延誤,請遵循以下指導方針:
準確的數據
無錯誤的組裝過程需要準確的數據。每個工作應該包含物料清單(BOM)、點位檔案(也稱為中心點檔案)以及相對應的Gerber數據。如果有元件不應安裝在PCB上,請在BOM中添加”DO NOT POPULATE”(DNP)欄位。
確保正確的封裝
某些元件有不同的封裝形式。請確保您在BOM中指定的元件與PCB上的封裝對應。
元件組織
元件應該分開放置在各自的袋子或托盤中。每個袋子或托盤應標註製造商名稱、製造商零件號,以及使用該元件的所有參考標識符。如果需要,可以用分銷商名稱和零件號代替(或附加於)製造商信息。
每個訂單的多個工作
每個工作的元件應分開包裝。每個工作應包含單獨的BOM和點位檔案。
元件數量
應包含額外的元件來應對可能的損耗。
小批量(1至25塊板)需要額外的元件數量如下:
- 0201至0603尺寸:至少多50個,外加所需數量。
- 0805至1206尺寸:至少多25個,外加所需數量。
- 對於大尺寸元件,1至2個額外元件即可。
- 我們建議所有SMT元件使用連續條帶或卷帶。
- 對於大批量生產,按百分比計算額外元件數量是可以接受的。
我們會將任何未使用的元件在出貨組裝板時一併退還給您。
更新您的BOM和點位檔案
如果您有任何臨時的設計變更,請記得在BOM、點位檔案和其他相關文件中反映這些變更。
標註極性
請確保為所有具有極性的元件標註正確的方向。對於極性不明顯的IC,在引腳1上放置一個點或數字”1″來標示。確保有極性的電容和二極管正確標註。
特殊指示
提供有關組裝板所需特殊程序的詳細指示。根據需要,請包括草圖、照片、PDF文件和/或圖紙。
PCB組裝過程
在PCB製造過程中,電路板的結構完全確定後,將進入PCB組裝過程。在PCB製造過程中,孔已經打好,為設計好的電子元件提供了具有特定尺寸的空間。在組裝階段,會依次進行多項操作,最終目的是確保電子元件牢固且永久地固定在電路板上。
模板準備
金屬片應覆蓋整個印刷電路板表面,除了稍後會填充焊膏的孔位。因此,金屬片必須根據工業設計的PCB圖案進行處理,金屬片上的孔位應與PCB上的孔位形狀、寬度和長度相同。這種金屬片通常被稱為模板,可以是黃銅或不銹鋼製成。
模板設計是一項高度具有挑戰性的工作,因為模板形狀的精度和模板厚度的一致性對於精確且有目的的PCB組裝至關重要。模板的典型厚度範圍為0.0254毫米至0.762毫米。金屬片的厚度取決於所使用的電子元件類型,並且每個印刷電路板的金屬片厚度是單獨確定的。即使是微小的尺寸偏差,也可能在後續的PCB組裝過程中引發重大問題。較大的模板孔位會導致所謂的”球化”或”橋接”現象,這些現象通常出現在焊接過程中,焊膏覆蓋了部分PCB表面,甚至在兩個相鄰孔位之間形成了整個連接路徑。這些現象會導致開路,使PCB完全無法正常工作。在選擇所需的模板參數後,我們會從金屬工廠訂購符合規定組成和厚度的金屬片,並使用X射線儀器檢測金屬片的厚度均勻性,然後將其送到我們的生產工廠。
化學蝕刻
模板處理技術有多種,但激光切割和化學蝕刻是最常用的兩種。在化學蝕刻過程中,金屬掩膜和柔性金屬掩膜會從兩側進行蝕刻。首先,PCB設計應使用膠片轉印到金屬片上。然後,將金屬片浸入特定的酸溶液中,通過蝕刻形成孔位。然而,該過程的缺點是酸液會對金屬片的較深層造成干擾,導致下切現象。因此,必須對牆壁進行額外的拋光處理,以形成平滑的表面,適合於PCB組裝過程中的焊接應用。牆壁平滑化有兩種方法:電解拋光和鎳電鍍。電解拋光是一種反向的電鍍過程,利用電流將過多的金屬溶解到電解液中,並在處理後清洗掉。而在鎳電鍍過程中,額外的金屬層被施加到孔位的牆壁上,導致孔徑減小。
激光切割PCB
在PCB組裝過程中,專用的CNC機器用於激光切割PCB。應用的激光束會根據Gerber文件中提供的圖案來切割金屬片。該文件包含PCB的所有技術規格,而集成的定制軟件會根據這些規格來導航激光切割過程。由於金屬的結合力極強,因此需要精細調整激光參數來創建平滑的金屬邊緣。激光切割過程中,以下參數對於切割的精確度至關重要:光束點大小、光束聚焦、切割速度和激光功率。激光功率必須足夠強,以便穿透金屬片表面。0.0254毫米的光束點是PCB組裝中最常用的,因為它適用於切割幾乎所有形狀和孔徑尺寸。無論設置參數的精確度如何,都需要使用與化學蝕刻過程相同的技術(電解拋光或鎳電鍍)來進行孔壁的額外平滑處理。
焊膏印刷
在PCB組裝過程中,使用一種特殊的印刷機來應用焊膏。這種印刷機通常被稱為刮刀印刷機。它的名稱來自於用來將焊膏壓過模板表面並填充到PCB孔位的刮刀。根據所需施加的壓力範圍,刮刀可以是金屬或聚氨酯製成。印刷機的內部視覺系統將模板垂直對齊在電路板上。此外,該印刷機使用三個基準標記,通常稱為全局基準標記,用於實現模板的最高精度定位。也就是說,全局基準標記在印刷操作前及印刷過程中,會立即檢測並修正可能存在的PCB錯位,無論是X軸還是Y軸。這樣可以完全避免在刮刀壓力作用下,電路板或模板的位移。
刮刀壓力是一個必須特別關注的參數。過高的壓力可能會引發多種問題,如焊膏剪切過大,導致焊膏在PCB表面擴散,並引起所謂的橋接或焊膏滲漏。由於焊膏是一種高黏度的懸浮液,它需要相當大的力量才能流動。刮刀的壓力必須足夠大,以克服焊膏與模板之間的高摩擦力。一旦焊膏開始移動,它會在可印刷區域的寬度上以受控的滾動方式移動,填充所有模板孔位,同時由刮刀刮去模板表面上的焊膏。刮刀的標準操作壓力範圍為每線性厘米可印刷區域0.13公斤至0.27公斤。移動的刮刀必須引發慣性,這樣焊膏才能流入PCB孔位。刮刀的快速而受控的運動會引起慣性,因此速度也是另一個必須持續監控的參數。由於刮刀的壓力與速度成正比,因此速度必須保持在上限值以下,通常為每秒75毫米。較高的速度會增加刮刀與模板之間的摩擦力,長期下來會導致刮刀的機械故障。
焊膏印刷的第三個關鍵參數是刮刀與模板之間的角度。常規設定的角度為60°,原因如下。這樣的角度形成了一個最佳的傾斜度,使焊膏能夠依靠重力向下流入PCB孔位。如果角度增加,會導致刮刀將焊膏從模板孔位中刮出,從而造成焊膏不足。相反,如果角度減小,刮刀在完成印刷後會在模板上留下焊膏殘留物。
每次印刷操作通常持續15至45秒。印刷是PCB組裝中時間最長的步驟,隨後是分離過程,即將模板從PCB上分離。印刷後的檢查對於確保焊膏層的質量至關重要,並且要確保焊膏適合於後續的電子元件表面貼裝步驟。質量保證通常會使用印刷機上的2D視覺系統或單獨的3D系統來進行。
模板分離與清潔
在印刷過程結束時,PCB會從模板中分離。在這一過程中,焊膏必須保持在PCB的孔位內。模板移除的速度至關重要,以確保模板不會從開口中帶走任何焊膏。模板的常規移動線速約為每秒3毫米。如果速度過快,焊膏無法完全從開口中釋放出來,會導致焊膏沉積周圍出現不期望的高邊緣。
經過幾次印刷操作後,模板清潔確保焊膏顆粒不會在模板和PCB之間積聚。清潔操作包括兩個步驟:首先,使用異丙醇等清潔化學品清掃模板,清潔模板底部區域。接著,進行額外的真空清潔,清潔模板開口,以避免焊膏流動受到阻礙,影響焊膏流入PCB孔位。
印刷後模板與刮刀狀況的質量保證
在對機械部件進行質量保證之前,會由自動清潔系統徹底清除焊膏殘留物,讓操作員能清晰地檢視整個材料表面。然後,操作員進行目視檢查,檢查模板和刮刀是否有任何機械故障。如果發現刮刀或模板損壞,操作員需要更換損壞部件,以確保印刷過程的可靠性與效率
焊膏成分、特性與儲存
成分
焊膏是由金屬焊料顆粒分散在助焊劑中的懸浮液。金屬焊料可由不同的元素組成,最常見的成分是99.7%的錫和0.3%的銅。金屬顆粒呈球形,且其大小根據IPC J-STD 005標準的類型而有所不同。過去焊膏中常使用鉛,然而,由於國際環保法規的要求,鉛的使用已被淘汰,因為它對人體健康和環境有極大危害。助焊劑則作為粘合劑,將金屬顆粒粘接在一起,並幫助電子元件安裝到電路板的焊盤上。助焊劑是一種高粘度材料,含有60%至80%的活性成分,這些成分有助於將金屬顆粒粘結在一起,並防止氧化與腐蝕。助焊劑中的大量活性成分能防止金屬氧化物在基材和填充材料上形成。
此外,助焊劑使得焊膏可以通過孔印刷進行焊接。按重量計,混合焊膏通常包含90%的金屬,但由於助焊劑的密度較低,非金屬成分占據了焊膏體積的一半左右。
特性
焊膏是一種非牛頓流體,更準確地說,它是偽塑性流體,這意味著當施加的壓力達到特定值後,其流動阻力會顯著降低。偽塑性行為是焊膏的關鍵特性之一,它使得焊膏能成功地進行印刷。由於流動阻力的顯著變化,焊膏在印刷過程中會進出模板的開口,但當印刷結束時,它會保持在PCB孔內,而不會下垂。
粘度是決定流體抗流動能力的物理性質。除了助焊劑中的化學成分外,金屬與助焊劑的比例對流動阻力影響最大。金屬含量的增加會顯著提高焊膏的整體粘度。在印刷過程中,刮刀和模板之間的薄焊膏層會經歷顯著的溫度上升,這會降低焊膏的粘度,因為這是由施加壓力引起的摩擦力的結果。
焊膏的儲存
適當的焊膏儲存能夠保持其所需的性能,以達到PCB組裝的最佳效能。焊膏必須儲存在密封容器中,以防止金屬與氧氣和水分接觸。金屬顆粒的表面積大,使其極易腐蝕,這會降低與電子元件接觸時的粘結強度。另一個需要控制的參數是溫度。儲存溫度應低於8°C,而1°C是最低溫度限制,因為助焊劑中含有液體成分,可能會結冰。控制儲存條件可以減緩金屬顆粒的氧化速率,同時降低熱敏助焊劑成分降解的速率。
電子元件安裝
當焊膏塗覆在PCB表面後,電子元件的安裝是通過所謂的點膠機來完成的。在啟動點膠機之前,必須通過將材料清單和元件放置清單上傳到Mycronic Mycenter工作站來編程操作算法。編程完成後,操作員將所有需要的電子元件供應給點膠機。此時,機器已準備好開始運作。在其運行過程中,元件安裝的精度是反映PCB組裝質量的關鍵參數。與刮刀打印機相似,點膠機使用三個基準點來定位面板並確定方向。基準點是刻印在每塊PCB銅層上的光學標靶。
每個元件都有自己的條形碼,機器可以識別,並將元件的位置信息發送至控制系統。除了識別元件及其位置外,該設備還能檢測元件的尺寸和安裝所需的旋轉角度。這台機器還會進行電子元件的質量保證,通過測量元件的電容、電阻和電感來進行檢查。如果發現元件的設計參數與實際測量參數不符,機器會立即將該元件移除。
固化爐焊接
當元件被放置到PCB表面後,它們必須被永久固定。這一固定過程是通過焊接來實現的,焊膏會首先熔化,然後硬化。在硬化過程中,焊膏內部的原子排列會發生變化,焊點的物理特性也會隨之變化,從而使焊接點具有高拉伸強度。熔化過程發生在固化爐中,PCB通過傳送帶進入爐內。加熱空氣的溫度通常在250°C至480°C之間,並以與傳送帶運動方向相反的氣流方式加熱PCB。由於焊膏的設定溫度能迅速達成,固化過程持續時間較短,隨後進入硬化過程。硬化過程同樣在爐內進行,空氣將熔化的焊膏冷卻並最終使其硬化。
檢查與功能測試
在PCB組裝完成後,操作員會進行目視檢查,確保所有元件正確安裝。目視檢查後,PCB會接入電源進行功能測試。在測試過程中,會模擬PCB運行的正常環境,如果沒有發現缺陷,則該PCB可以準備出貨。
保形塗層
表面處理塗層是一個重要的步驟,用來保護元件免受不同環境因素(如濕氣)的影響。
表面處理塗層會塗覆在電路板上,形成一層屏障,隔絕污染物與PCB之間的接觸。同時,它還會創造一層絕緣層,減少板內的串擾、漏電流以及電化學遷移。塗層材料可包括丙烯酸樹脂、聚氨酯、矽樹脂、環氧樹脂,或多種樹脂的混合物。
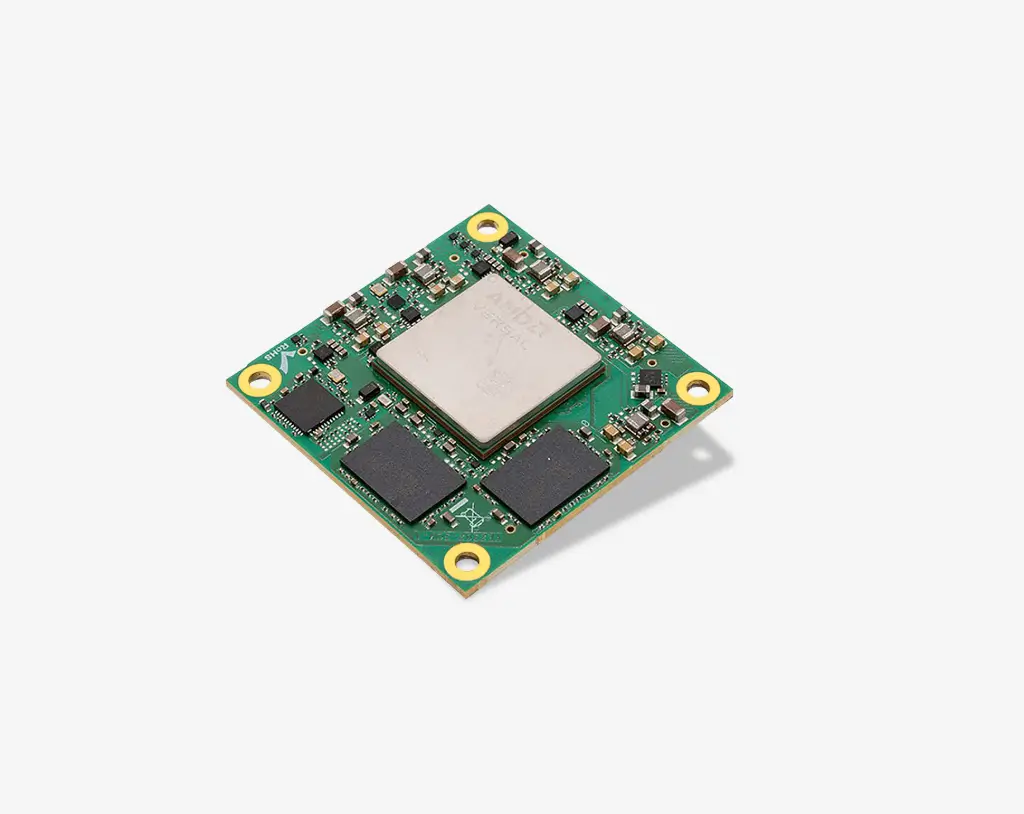
高品質PCB組裝
PCB組裝過程發生在PCB製造完成後,此時電路板結構已根據客戶需求完全形成。PCB組裝涵蓋從模板準備、焊膏印刷,到SMD元件安裝、固化爐中形成焊點、以及最終的PCB功能檢查等一系列動作。模板準備完成後,進行焊膏印刷。在此階段,微小的開口需準確無誤地填充焊膏,這些開口是用來安裝電子元件的安裝點。如果焊膏印刷不夠精確,可能會產生如橋接等嚴重問題。橋接通常是微小的,肉眼難以察覺,因此如果不使用先進的檢測設備,往往很難檢測出來。然而,這仍然是PCB組裝過程中最常見的問題,可能會導致短路,甚至元件燒毀。因此,我們奔創電子使用最新的焊膏印刷技術,確保每一塊印刷電路板在組裝線結束時能夠正常運行。
開始了解印刷電路板組裝
- 整機組裝
- 整機組裝
- 軟性PCB組裝
- SMT實裝、BGA實裝、通孔實裝、混合實裝